Tuck away your pop culture perceptions of lasers for a moment: lasers are good for more than exploding planets and making pew-pew noises in Sci-Fi action films.
Despite being around since the 1960s, laser die cutting has clung to its title as one of the most accurate and automated design modes. With how fast modern technology advances, lasers often improve traditional metal-cutting equipment or replace it entirely.
At Strouse, we do rapid prototyping for our clients using laser die cutting to build accurate samples, and we also do full-scale production. When you finish this article, you’ll know how die cutting functions, the benefits, and why it may or may not suit your project.
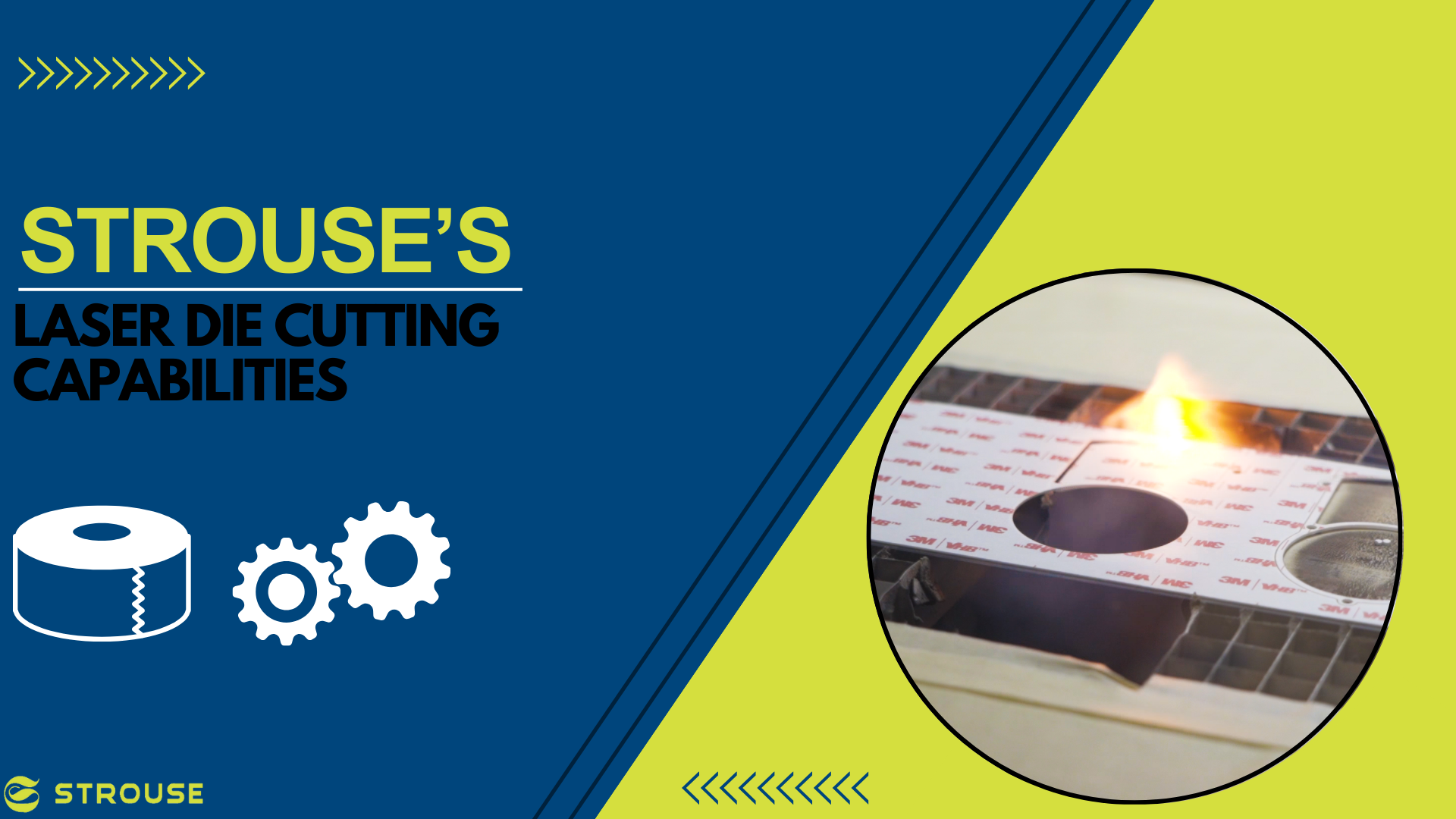
What is Laser Die Cutting?
Laser die cutting is the process of using a high-speed laser to cut out parts. These parts are often relatively small and require skillful precision beyond flatbed or rotary die cutting tooling, hence the laser.
How Does Laser Cutting Work?
We’ve all seen fictional lasers in movies and TV shows, but how do lasers function in the real world?
All lasers emit a beam of light channeled from an energy source into an optical cavity, which then directs it. However, the technical details depend on which type of laser you’re using.
GAS LASERS
The most common type of gas laser is the CO2 laser, which is used for pretty much any material (even skin!) except for metal.
The CO2 laser works by mixing helium-nitrogen-carbon dioxide gas and introducing it to water vapor and other elements.
An electric current is sent through the mixture to excite the nitrogen, which collides with low-temperature helium atoms to produce photons through resonant energy transfer.
The photons flow into the nozzle and are reflected in one powerful light beam. After it’s concentrated into one point, this beam becomes a laser that can cut through solid objects.
FIBER LASERS
In a fiber laser, the beam is typically straight and precise, cutting through various materials, including different metals.
Fiber optic lasers are used in welding and cutting and have other unique advantages, like a low maintenance cost and high electrical efficiency.
The most significant advantage of using a fiber laser is its optical fiber cable method to narrow down the size of the beam. This smaller beam is more precise than other lasers.
Single-mode optic fiber cables are difficult to manufacture or handle, but they are relatively small and transfer signals quickly. Your other option is multi-mode optic fiber cables, which are easier to manufacture and control but only used for short-distance purposes.
Lastly, the size of the core (also known as the mode) of a fiber laser determines the effectiveness of its light delivery and the overall beam quality.
CRYSTAL LASERS
Also known as “solid-state,” these lasers use transparent solids, like crystal or glass, to emit maximum light amplification.
The most popular kind of crystal laser is known as the Nd:YAG laser, or neodymium-doped yttrium aluminum garnet laser, and is often used to get rid of unwanted birthmarks or scars.
Crystal lasers are used in the medical field for procedures such as tissue ablation, the removal of dental caries, and tattoo removal. They can be very powerful but wear down quickly; thus, the machines are expensive to maintain.
Pros and Cons of Laser Die Cutting
Like any process, laser die cutting has different strengths and weaknesses, so you should carefully consider your options before deciding which method is right for you.
PROS
Numerous industries use laser die cut parts, but perhaps one of the most common proprietors is medical.
The medical industry has an extensive past of using laser technology to treat patients. Not only do doctors use lasers to treat skin cancer and severe acne, but laser die cut parts also make up the intricate parts inside fluid diagnosis tests.
One of the most significant benefits of laser die cutting is the tight tolerances. This is perfect for applications in microfluidics, where devices require much narrower, more complex margins than any die tool can achieve.
The production of a single part may be limited by its irregular shape or the size of its measurements. However, a laser is more versatile than a solid, cookie-cutter-like mold and could easily circumvent either issue.
Another perk of laser die cutting is the ability to stack different materials before slicing them.
Layering parts is helpful because it speeds up the assembly process and provides a safeguard by covering the pristine bottom material and helping it escape scorch marks. Because they were cut into each other, these layered parts should fit together cleanly and precisely.
The risk of scratching is non-existent since the laser’s nozzle never touches the workpiece. Aside from the laser itself, laser die cutting is small-tolerance and can be contactless, making it a popular choice for delicate, medical-grade parts.
CONS
If you’re building a million parts, you might want to take a seat: they’ll take a while to laser cut.
Many materials must undergo multiple passes of the laser, doubling, tripling, or even quadrupling the time it takes to produce each part. Also, the laser’s speed must match the number of movements it makes during each pass. As a result, laser cutting will likely require more time than a rotary die press.
Materials can also be difficult to laser cut due to their natural thickness and flammability, like foam for example. Assuming the foam doesn’t initially melt or catch fire, its width becomes the enemy of accuracy and efficiency.
The wider or thicker a part is, the more the laser beam will diverge upon impact, creating a slight incline in the cut itself, referred to as the draft angle. Draft angles often correspond with the width of a material, making them an essential element for cutting out thick parts.
Another factor to consider when slicing thick parts is what’s referred to as the kerf, or the percentage of material obliterated by the laser the instant it gets struck.
Kerf is predictable, but including it in your initial material estimate is crucial to ensure you begin your project with the correct supply.
Finally, lasers can be tricky to fine-tune regardless of the quantity you plan on producing. Determining the depth of a kiss cut may take some trial and error, depending on the laser’s settings and the material size you need to cut through.
Unfortunately, the term “trial and error” implies losing time and money, so finding a converter with enough experience to breeze through the testing phase of laser kiss cutting painlessly is essential.
Why You Should Use Laser Die Cutting
Outside of physical capabilities, there is still a crucial cost-benefit analysis to weigh.
Spending much of your budget on an expensive, highly specialized metal tool doesn't make sense when you only need fifty parts. Why not build them with a laser?
Operating a laser isn’t always as fast as punching out shapes on an assembly line, but it can be a fantastic way to save time and improve production for smaller jobs. Rather than using a considerable stretch of time to design and build the perfect tool, it might make more sense to use a laser.
If you’re considering using laser die cutting for your application, you can find out more about it above. Otherwise, you can discover more about cutting flexible materials in our Learning Center.
Originally published: August 11, 2022
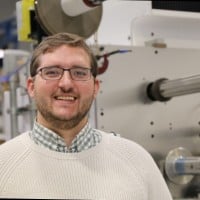