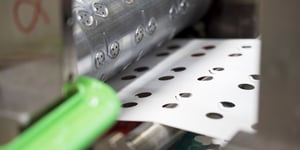
ROTARY DIE CUTTING
Cut Exact Lengths, Tight Tolerances
Rotary die cutting uses custom-shaped blades mounted on a cylinder to cut out parts at a rapid pace. The die tool rotates in tandem with the material to cut exact lengths every time.
The primary advantage of using rotary die cutting is to process a high volume of material in roll form for larger projects.
Request a Quote Learn More About Die Cutting

What is Rotary Die Cutting Used For?
Rotary die cutting is the most efficient method of die cutting high volumes of material on a roll. It is a reliable choice for larger projects that may require multi-layer cutting scenarios, including:
- Seals and gaskets
- Protective films
- Labels
- Medical adhesive tape
and many other products.
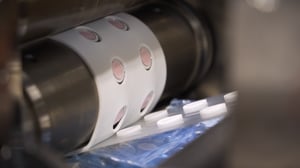
Plan your project budget.
The Benefits of Rotary Die Cutting
- High volume at high speeds
- Clean cuts of identical shapes
- Deep or multi-layer cuts
- Tight tolerances using servo motors to maintain registration
Operators feed the material through the machine press and die station, where a custom rotating blade mounted on a cylinder cuts the material. The die tool spins in tandem with the material feed speed so it can cut precise shapes and lengths.
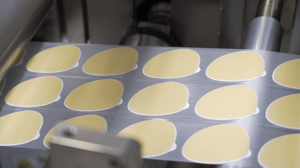
We can help you select the right method for your needs.
Get a Rotary Die Cutting Quote
Provide us details in the form and we can get you a quote for your product.
- What Product Are You Looking For?
- What Size/Dimensions?
- Quantity You Will Order
- Information on How the Material Will Be Used
- Problems You May Have Encountered When Using this Material