If you’ve ever been in a discussion with a converter about die cutting, you might’ve heard the phrase “kiss cut” before.
Funnily enough, you’ll find that asking about the difference between die and kiss cutting is the equivalent of asking the difference between a square and a rectangle.
Kiss cutting is a critical technique that Strouse and many other flexible material converters perform daily.
Before you go into part production, learning about basic converting processes like kiss cutting is crucial to understanding how they benefit your design.
What is Kiss Cutting?
Kiss cutting, also known as “pressure-sensitive cutting,” is a type of die cutting where the blade does not penetrate the entire stack of material but instead cuts through a precise number of layers.
Depending on the pressure between the die and the material underneath, you can create a setup where the die's sharp edges only penetrate to a certain depth. This process allows for complex product creation with accessible options for easy peeling.
KISS CUTTING EXAMPLE
One example of kiss cutting would be building a sheet of kiss cut stickers: the blade goes through the sticker layer with the design but stops before puncturing the liner, allowing the sticker to remain on the intact backing.
The slicing depth can be calculated to the millimeter; therefore, it's possible to remove the top layer of material and leave behind a specific shape attached to the backing.
What is Die Cutting?
Die cutting punches specific shapes from sheets of raw material as it runs through the factory press. Depending on the tooling of each project, the die cuts could be kiss cuts OR through cuts (a.k.a. metal-to-metal cuts).
Unlike kiss cuts, through cuts pass through ALL the layers of a material and make contact with the metal anvil.
Die Cut vs. Kiss Cut: Which is Better?
You might be asking yourself, “Okay, so if kiss cutting is a TYPE of die cutting, then should I use it for my project?”
Referring back to our analogy, all squares are rectangles, but not all rectangles are squares. All kiss cutting is a type of die cutting, but not all die cutting is kiss cutting.
- Die cuts:
- A combination of through and kiss cuts
- The blade can pass all the way through
A finished product with its main body attached to the liner would result from the combined kiss cutting and through cutting.
- Kiss cuts:
- Are a technique used in die cutting
- The blade never passes all the way through
Kiss cuts are valuable tools in die cutting projects, especially through direct application on the rotary die press. Yet, kiss cutting isn't limited to a rotary die cut press and can be implemented in alternative die cutting processes.
- Through cuts:
- Are a technique used in die cutting
- The blade passes all the way through
Kiss cutting can consolidate the steps of an otherwise tedious process when used in tandem with through die cutting. If you need to cut specific layers of material, kiss cutting might be the best choice for you.
LASER KISS CUTTING
Laser kiss cutting uses a weakened laser to make shallow cuts in a material. Because the laser's actual power is adjustable, the beam strength can be lowered so it doesn't cut all the way through.
Depending on the project, however, a laser might not be the ideal tool to use in certain situations because using a laser involves searing off material, which may have dire consequences for certain adhesive materials (i.e., liquifying them).
Disadvantages of Kiss Cutting
While kiss cutting can be an excellent die cutting method to boost project efficiency, it will not be simple for every project or material.
- Requires close monitoring
Kiss cutting requires close monitoring so that each cut is made precisely. If done incorrectly, kiss cutting might render products imperfect or even unusable.
If the kiss cut is too shallow, which may be difficult to spot initially, the product might not work. However, if the cut is too deep, the adhesive can enter the gap and cause problems between the material and its backing. It can also cause “deep die strikes,” which leave an imprint on the liner below the material.
- Risk of imperfect rolls
Defective kiss cutting may create imperfect rolls that are sloppy in the placement of their parts due to shifting during the delivery process. These imperfect rolls also risk possessing inconsistent tension, which might hinder any automation the product needs to undergo.
Getting Started with Die Cutting
If you believe die cutting is right for you, then it might be time to reach out and find a converter that can help.
The first step in figuring out your custom die cutting process will be looking over your entire planned process with a converter and optimizing the production. Consider scheduling a consultation to begin.
For more information about die cutting, check out our Learning Center.
Originally published: July 19, 2022
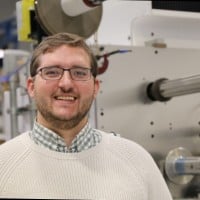