You may have heard the term in manufacturing before, but let’s define it: What is die cutting?
You’ve got a part that needs to be bonded, masked, protected, etc., so you must add adhesive, films, foams, or soft metals to your assembly. The raw material must be cut into a particular shape to generate a finished product. However, nobody has the time to sit around and fiddle with a pair of scissors. So, what’s the solution?
That’s where die cutting comes in.
Die cutting starts with the process of outlining your desired shape, which is then crafted into a 3D stencil, called a die, and attached to a press. The stencil is brought down on top of your raw material to punch out the shape you need, similar to the concept of using a cookie-cutter on dough.
The die cutting process can be used to cut many different materials, including but not limited to:
- Paper
- Plastic
- Fabric
- Adhesive
- Foam
- Soft Metals
Die cut adhesives often provide many advantages, such as demonstrating fewer product errors and simplifying a complex process into a single line of steps, preventing headaches and saving you hours of production time.
When it comes to die cuts, the force is distributed evenly along the entire bond, which minimizes stress points and ultimately results in less failure. Additionally, die cuts create secure physical seals, allowing for some flexibility regarding temperature changes. This is a considerable advantage when constructing a vehicle that can be used in various climates.
The right converter for your purposes will know what questions to ask about the material and application so that each finished adhesive can withstand the minimum amount of stress.
Complex materials, such as those flexible or sensitive to pressure, might be difficult to handle without a converter. It will require a capital investment into machinery and tools, and there will be an investment to acquire the know-how to get it all done. However, converters like Strouse process a wide range of flexible, pressure-sensitive materials every year, some of which must be die cut in a specific environment based on factors such as humidity, particulate count, or even light exposure. By working with a converter, you can tap into all of that knowledge and experience.
There are two factors to consider when discussing the production of die cut adhesives: The adhesive’s purpose and Which die cutting method will produce the best possible solution.
When discussing purpose, there are lots of situations and industries that discover great value in using die cut adhesives.
Medical Die Cut Adhesives
Many industries rely on the consistency of die cut adhesives, but few are as crucial as their application in the medical field.
The human body can contort in a wide range of motions, which makes it challenging to develop products that can adequately conform to the shape of each patient’s skin. However, die cut adhesives can support each body type and present the best possible wound care due to their accurate sizing capabilities.
Medical adhesives often adhere closely to the skin. If the wrong adhesive is used, it can be difficult, if not downright painful, to remove.
Examples of medical die cut adhesives include products made to:
- Stick a device to skin
- Deliver an active ingredient through the skin
- Cover a device
- Hold device components together
- Move fluid
One advantage of medical die cut adhesives is the breathability achieved through specialized materials. This factor can be combined with pressure sensitivity to make the most efficient and painless adhesive solutions.
As you collaborate with a converter during the manufacturing process, the more extensive selection of raw materials will allow you to make better decisions based on each adhesive’s unique capabilities rather than accepting whatever happens to be in stock.
Automotive Die Cut Adhesives
Automotive suppliers are one of the biggest partners in converting due to the sheer amount of die cut adhesive parts used in an automobile’s construction.
Here are some of the most common automotive adhesives:
- Gaskets and Sealing
- Paint Masking / Masking Kits
- Transit Protection
- Surface Protection
- Hole Covers
- EV Solutions
In 2021 alone, 8.8 million motor vehicles were produced in the U.S. With the automotive industry continuing to grow over time, the speed and precision of die cut production has transformed die cut adhesives into an efficient solution to many common problems automotive companies experience.
One example of an EV solution would be when Strouse partnered with Tesla Motors to develop a feasible, cost-effective solution for the battery connection assembly process. Strouse used a die cut adhesive to reach the brittle and layered mica shields within the battery, which fixed the issue of their adhesive transfer.
Adhesive die cutting is essential to the automotive industry due to the durability of the pieces being produced. Most consumer-based motor vehicles are built to last, so your customers must never fear the adhesives will wear out.
Die Cut Consumer Goods
The history of die cutting is based on the production of consumer goods.
Cobblers invented the process of establishing accurate leather cuts, which determined standard shoe sizes. In the modern age, however, standardization is another factor products need to reach widespread success.
When creating a water-resistant video camera, Strouse was able to bond multiple components using a die cut adhesive, which resulted in the successful prevention of water leakage. In this case, the die-cutting method was efficient enough for the adhesive to be made in bulk, enabling the cameras to be readily produced.
On the other hand, many artists use die cutting to create products such as:
- Logos
- Flyers
- Decals
- Book cover surface protectors.
One of the most significant challenges facing the creative side of commercial production is the issue of maintaining standard measurements. A substantial proportion of these pieces are constructed by hand, yet an abundance of product errors may turn receiving customer satisfaction ratings into a monumental task.
Die cut adhesives have proven themselves a strong industry competitor, as they can be produced at different scales while remaining identical to one another.
These are just a few examples of the many times in which adhesive die cutting is used for manufacturing, but there are plenty more. Click here for more ways on how die cutting is used!
As great as it would be to use a single machine for every process, there are multiple ways in which different materials can and should be die cut.
The final factor to discuss when it comes to adhesives is the different die cutting methods.
Flat Bed Die Cutting
The cutting die is set inside a hydraulic press, which then raises and lowers it vertically to stamp out shapes from the material like a cookie cutter. Either the die or other tools can be swapped out without much hassle, so quick and simple projects are the way to go.
Low-volume projects are perfect for flatbed die cutting because they can be finished at a fast rate, which might save time and money.
Suppose a product isn't coming out correctly on a rotary or laser cutting machine. In that case, the flatbed die cutting method may be a reliable and straightforward alternative, especially for very extensible materials.
Rotary Die Cutting
Remember our cookie-cutter analogy? Imagine lining up multiple cookie cutters in a row and attaching them to a rolling pin.
The rotary die cutting method can produce objects at a much faster rate due to the continuous motion of the cylindrical die. The material is fed through at an exact rate, allowing for tighter tolerances, and is often monitored electronically so adjustments can be made.
The steady nature of the rotation leads to the creation of many identical, highly precise parts, making rotary die cutting the standard for medical, military, aerospace, and many other industries.
Laser Die Cutting
As the name suggests, laser die cutting requires no blade and consists of controlling a high-speed laser to make the cuts. It’s a programmable process, which can be repeated as often as needed, with the potential to create the tiniest details and tightest tolerances you may need.
Laser die cutting is especially useful when cutting flexible materials to prevent mistakes from being caused by the motion of the steel die.
Adhesive die cutting has become an essential tool for converting, and it applies to a wide variety of industries. As a leading convertor, Strouse is committed to keeping up with the latest information and technology of the daily processes we perform.
If you are interested in this topic, we encourage you to Learn more about what we do with die cutting and explore the many ways we might help you succeed.
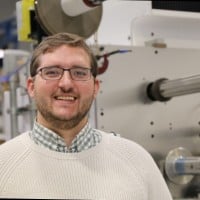