If your current assembly method is outdated, experiencing quality issues, or open to improvement, then die cut adhesives are an excellent tool for advancing your current process.
As a material converter that specializes in complex die cutting, Strouse helps our customers realize production efficiency on a daily basis from our die cut solutions.
Whether you’re actively seeking a converter or simply browsing your options, this article will give you a better idea of how die cutting may help your business.
Using Adhesive Tape Die Cuts To Advance Your Production Process
Adhesive die cuts are near-identical components cut from flexible materials using steel die cut tools. Here are the benefits of using them in a manufacturing process.
-
INCREASED EFFICIENCY
Arguably, the most significant advantage of die cut adhesive tape is the efficiency it can bring to a production process.
Die cut parts are uniform components that are often paired with adhesive design features for rapid application. They are easy to use during part assembly and typically far quicker and cleaner to apply than alternatives like liquid adhesives, which require time to dry.
-
CONSISTENCY
The uniformity of die cut parts creates a more consistent and replicable process, which can help reduce errors, defects, and material waste during production. It might also save the time it would take to correct said mistakes.
-
REDUCED COSTS
Die cutting machines can produce adhesives faster and more accurately than any employee with a pair of scissors. Rotary die cutting is especially ideal for producing custom adhesives en masse, which saves machine run-time and labor hours.
The die cutting process also allows converters to condense multiple steps to simplify part construction and packaging. Additional steps like printing and adhesive laminating can be performed on the same press to save time and reduce costs.
Consolidation is the key to avoiding high shipping costs. There’s no need for an adhesive part to be painstakingly cut out, sent hundreds of miles for lamination, and then transferred back for packaging before it goes out to the final buyer. Instead, a converter could invent a one-step-production setup to rapidly construct a finished part.
-
EASIER PATH TO AUTOMATION
Automation uses advanced technology to innovate the manufacturing process, typically used to fulfill repetitive tasks on behalf of workers.
A company must trust that the smaller parts have consistent measurements to succeed in automation. Die cut adhesives are manufactured in bulk and share the same dimensions as the rest of the batch. This allows product assembly to run faster and makes the products more accessible for customer use.
Automation can be as simple as kiss cutting crack-and-peel liners or pull tabs onto an adhesive for easier part application. Converters also use automation during product packaging, which is often done automatically. Packaging straight off the press will save time and reduce skin-to-product handling, which is handy for many medical devices.
The Benefits of Each Die Cutting Method
There are three primary methods of producing adhesives on a large scale: Flatbed, rotary, and laser die cutting. Each method has advantages and disadvantages, so it’s essential to understand the part dimensions and their intended use before deciding which will work best.
Factors to consider are the part tolerance, the type of material, and the scale of production. Jobs with a tight tolerance require heavy detail and can’t withstand many discrepancies before becoming unusable. However, due to their size, they often suffer the most mistakes. If you need many parts, a method more suited to rapid production is worth considering.
a. FLAT BED CUTSFlatbed die cutting occurs when a die is lowered onto a static material from above. It is the simplest form of die cutting and has multiple advantages.
✔️ Create parts with larger dimensions
One advantage of flatbed die cutting is size capabilities, primarily the ability to create parts with larger dimensions. Certain pieces are too wide to fit onto a rotary press but might fit underneath a flatbed die.
✔️ Don’t suffer press tension
During flatbed die cutting, the material is static, so it doesn’t suffer the same tension as when pulled through a press. Changes in a material’s stress will alter the length of the cut ever so slightly, which will influence the final product.
Unfortunately, the pauses in between cuts mean that flatbed die cutting can be slower than other die cutting methods. Also, a flatbed press is typically one station, meaning it’ll take multiple steps to create your finished product. A single adhesive piece could be transported to various stations for printing, cutting, laminating, etc.
Flatbed die cutting could be the most effective strategy if you’re looking for the best manufacturing process to create accurate, small to mid-sized batches.
b. ROTARY CUTS
Rotary die cut parts are produced when the material is run underneath a cylindrical die. Rotary die cutting is an excellent option if you’re searching for a quick and efficient production method.
✔️ Make large quantities
The continuous motion of the rotary die can create a large number of custom die cut adhesives. Still, the constant press tension makes it less suited to cut materials like foam or stretchy polyurethanes.
✔️ Suitable parts for automation
Rotary die cutting can be a highly innovative process for creating parts because it lends itself to automation.
✔️ Combine multiple steps
Multiple steps can be taken at one station: Parts can be brought through a printer before getting cut, eliminating the need for back-and-forth transportation.
c. LASER CUTS
While it doesn’t technically use a die tool, laser cutting is a prevalent choice for flexible material cutting projects.
✔️ High-precision & Tight tolerances
Laser cutting can achieve the tightest tolerances, making it your best strategy if your adhesive design includes detailed features with precise measurements.
✔️ Easy to prototype
Using a laser is far cheaper than purchasing custom hard tooling, which makes it an excellent choice for early-stage designs and prototyping.
However, the laser cutting process tends to be slower than its alternatives. Instead of punching out a part in one motion, the laser must trace its way around each shape, which requires time. For this reason, laser die cutting isn’t as popular for mass production.
To determine if laser cutting is ideal, consider the type and thickness of material. Some materials (such as metals) shouldn’t be laser cut with a CO2 laser. Too thick or dense materials will cut slowly, and the laser angle could bend while passing through them.
Getting Started with Die Cut Adhesives
If you want to start using die cut adhesives, then you’ll probably have the best luck reaching out to a converter.
While some companies can purchase die cutting machines and move the process in-house, the steep initial investment and learning curve typically make it more worthwhile to outsource the job.
Contact Strouse today to get started with die cut solutions. We’ll help ensure that your production process has the tools it needs to succeed.
Lastly, if you want to know more about die cutting, you can find additional resources in our Learning Center.
Originally published: August 4, 2022
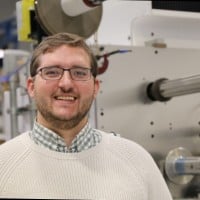