As you’ve likely noticed, rising demand for electric vehicles has led to increased battery innovation focused on increasing design and performance efficiency.
However, while simplifying the design and assembly process can lower the total cost, it requires a high level of technical expertise. Certain products can achieve ~30% higher energy density and lower cost by connecting cells to the battery pack directly, but this necessitates specialized adhesives.
Strouse is constantly finding new ways to manufacture challenging adhesive components for EV batteries, optimizing the existing design and materials until you can progress from prototype to production.
If you want to learn how to improve your design using die cut solutions for EV batteries, this article will discuss how they might benefit you.
Die Cut EV Solutions
EV batteries often consist of cells bound in modules that combine to form a battery pack. Therefore, EV battery construction involves many surface areas and connections between dissimilar materials.
Die cut parts for EV batteries can be used as:
- Bonding components
- Thermal and electrical insulation gaskets
- Cell separators & Gap fillers
- EMI shields
- Battery heat shields
- Thermal runaway protection materials, and more!
The following sections will cover the solutions that these applications provide.
1. BONDING CELLS AND MODULES
Die cut tape can be a rapid assembly aid and immediate bonding solution for EV battery applications.
Manufacturers can use die cut parts to instantly bond tiny components or entire panels of material without the mess of liquid adhesives or the added weight of mechanical fasteners.
- Liquid adhesives take longer to set than adhesive tape (which holds instantly on contact) and are difficult to apply precisely.
- Mechanical fasteners (like bolts, screws, or rivets) are heavy and at a higher risk of metallurgical contamination and rust.
Double-sided die cut tape contains multiple substrates, allowing you to join dissimilar materials. Surface connections between cells and modules are often between different materials, such as ceramic and mica, making it the perfect double-sided use case. For instance, Strouse built a solution for Tesla Motors to attach multiple layers of mica during the EV battery assembly process.
2. INSULATING INDIVIDUAL CELLS
Electrical insulation involves wrapping conductive components within the EV battery to prevent arcing or shorting. The protective die cut parts form a material barrier to separate the different layers and prevent misconnections from harming the battery.
EV manufacturers use single or double-sided tapes for cell insulation:
- Single-sided tape can attach to dielectric strength parts or materials, which are often ridged and geometrically complex.
- Double-sided tape combines compression pads and panels to maximize the insulating effect.
3. EMI SHIELDING
EMI and RFI shielding involves applying die cut layers to EV cells or modules to prevent electromagnetic interference from disturbing other vehicle apparatuses such as the main display, radio, or backup camera.
Electric vehicles host many onboard systems for safety, navigation, and fueling, but interference from the EV battery can cause these systems to malfunction.
Die cut EMI shielding parts are typically made from materials like copper and aluminum and can be found as EMI gaskets, films, or foils. These pieces cover whole surfaces to avoid signal leakage, and their application method is highly precise.
4. GASKETING AND BATTERY PROTECTION
Moisture and other contaminants can devastate an EV battery, so a tight seal is crucial for any assembly. Many manufacturers use die-cut gaskets to prevent moisture from reaching the electrical battery components.
Many electric vehicles contain dielectric liquid cooling systems and other fluids that could cause significant damage given a leak. Leaks in the battery pack can harm the internal components, reducing the battery’s lifespan and increasing the risk of failure.
Die cut gaskets inside batteries fill gaps and seal off the electrical parts. Converters often use flame-resistant material to build EV battery gaskets for added protection in case of thermal runaway.
5. REDUCING THERMAL RUNAWAY
EV batteries have the potential to overheat, which can cause catastrophic damage to the electric vehicle. If one individual cell is damaged and starts burning, the fire might spread to other cells and create a thermal runaway.
Thermal runaway is the worst-case scenario for an EV manufacturer. Once the excess heat has escaped the cell, it can result in burning, melting, and explosions: not ideal for any driver.
As a result, many batteries use die cut parts to protect the individual cells from thermal runaway by bonding cells to composites that reduce the risk of total failure. Flexible material converters create die cut parts using materials like flame-resistant PETs or polyamides for thermal management.
How Can Die Cut Parts Extend EV Battery Life?
EV batteries are full of delicate components that require effective, lightweight connections to ensure healthy battery life.
Die cut parts elongate EV battery life by:
- Keeping components bonded
- Insulating and padding against physical damage
- Shielding from interference
- Trapping out moisture
- Reducing thermal runaway for battery protection.
Prototyping Die Cut EV Battery Solutions
EV battery manufacturers build new products using custom part components that fit together, which may require adjusting some of the materials and designs.
By using a converter to rapidly prototype designs and materials, you can sort through your design options more quickly and accurately than by using hand-cut samples.
If you’re planning to design EV battery components, you’ll want to discuss your plans with a converter to prove out concept and find the right material and process. Reach out to a converter for samples today, and you can test your part with suitable material to see whether it adds value to your EV battery design.
Originally published: April 10, 2024
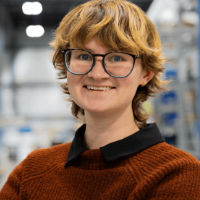