What would you do if your boss emailed you a picture of a circle without context?
You’d likely send back a series of question marks or a question like, “Do you need more table coasters?”
In all seriousness, while you know converters can’t produce your design without context, crucial details often slip your mind when the part is so familiar to you.
Strouse’s engineers collaborate with each of our clients to optimize their designs into the most production-efficient parts possible. Once you’ve reviewed these questions for the design phase of your project, you’ll be fully ready to answer technical questions adhesive converters will ask about your product.
Preparing for the Design Phase of Your Die Cut Part
It’s tempting to dive straight into the design phase of your die cut part, but rushing to begin is a guaranteed way to end up with late-stage production issues.
You may not realize that many parts are specifically designed with the intention of die cut converting.
By turning your idea into a first-draft design, you’ve already built it to a point where an adhesive converter can evaluate it and give expert advice on maximizing your production throughput.
3 Questions to Ask Before the Design Phase of Your Die Cut Part
We’ve all had meetings that feel like a series of “I’ll get back to you on that” playing on repeat.
Want to be better prepared for future questions your adhesive converter asks? Read through the following questions about your design to understand how to address their concerns.
1. WHAT ADHESIVE MATERIAL DOES YOUR DIE CUT PART REQUIRE?
While you don’t need to know the exact material, having a general idea will transform confused emails into more effortless conversations.
Although your adhesive material changes the specifications for your entire design, many first-drafts are created assuming that converters can substitute material at a moment’s notice.
Unfortunately, the type of material greatly affects how your part is processed. For example, foam stretches on the machine press, often making it unsuitable for incredibly tight tolerances.
Early-on consulting with your converter will enable you to choose the right substrate. Plus, if you wait too long to decide on your final material, you could get far into the design process only to realize it will be a struggle to find somebody to get the job done.
Instead of hesitating because you’re afraid of producing the part wrong, you have the option to test part ideas through samples to find the material that fits your design:
Many misconceptions hinder the design process: Thicker adhesive isn’t always stronger and asking for a thick material instead of a strong adhesive can get unnecessarily pricey.
Working with a converter to choose a particular adhesive material and being willing to consider design adjustments can make a huge price difference.
2. IS YOUR DESIGN FUNCTIONAL FOR DIE CUTTING?
Your part design might look uncomplicated when producing a single sample, but how will it work when you grow from making thousands of parts to millions?
As you scale up adhesive production, functional part design becomes necessary for an effective die cut manufacturing process. If your part design isn’t die cut-friendly, you risk complicating certain features or determining ultra-tight tolerances.
Overly-complicated part designs increase the die cut cost because converters pay more for complex tooling. Tooling costs can get up to $100k+ for the most complex tools. However, relatively simple tools can be as little as hundreds of dollars. Also, overly-complicated part designs can cause issues such as more material waste, which weighs down the cost over time.
Another aspect of design functionality is ensuring your part can be easily applied.
If you haven’t thought about how you plan on applying your die cut adhesive, it’s worth considering before meeting with your converter. Will your adhesive part need tabs or a particular liner? Is the process going to be automated at some point? Are you okay with parts on a roll or do you need them sheeted? Additional features will affect the price AND the process, so they’re worth asking about upfront.
Functional part designs cause the manufacturing process to run more smoothly and save you money. If you’re unsure how to check if your plan is practical or how to build a functional design, feel free to reach out for help with an adhesive part or idea.
3. WILL YOUR PART NEED TO BE STERILIZED?
Most non-surgical medical applications likely won’t require the highest level of sterilization many converters offer, so it can be challenging when deciding whether to pay for a part to be sterilized.
Still, if your adhesive is at risk of being tainted or ruined by biological particles due to its purpose, you might want to consider using a cleanroom.
An ISO 7 cleanroom uses a filter that allows it to undergo air changes rapidly, making it more than 100 times cleaner than a standard room.
This level of sterilization is necessary for certain devices, like DNA kits, but it comes at a higher price. It’s useful to clarify whether your part requires intense sterilization to determine whether cleanroom use is right for you.
Should You Plan Your Die Cut Design with the Help of an Adhesive Converter?
It’s tempting to design the part first and then seek out a converter who can build your finished product, however, it improves the overall cost-effectiveness of your design to bring in a converter as an early addition to the design process.
Not only do well-designed products come out more quickly because you can run them faster, but generally, quality checks run more smoothly due to fewer errors in the parts.
If you’re looking to learn more about the long term benefits of bringing in a converter early, check out all of the ways it may help your design:
If you already have your design started but are wondering how your product might behave on a press, feel free to evaluate your drawing to see what a converter says about press design and how it could affect your part’s intended purpose.
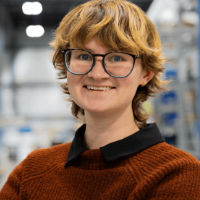