Do you know which type of bonding material to use in your project?
Two of today’s most popular are adhesive tape and liquid adhesive. However, both types of bonding materials have advantages that make them well-suited for their respective purposes.
While Strouse admittedly specializes in cutting adhesive tape and other flexible materials, we’re also well-versed in liquid adhesives. If you’re working on a project that involves bonding, you should also understand the difference between adhesive vs. glue to ensure you make the best choice.
Today, we will compare adhesive tape with liquid adhesive and discuss which one you should use for the sake of your project’s performance. You’ll learn about their pros and cons and understand the differences well enough to decide.
Adhesive Tape vs. Liquid Adhesives—Dividing Factors
While adhesive tape and liquids are powerful and effective bonding solutions in their own right, they each have their respective applications.
- Adhesive tape consists of a pressure-sensitive adhesive often attached to a paper or film backing.
- Liquid adhesive encompasses a wide variety of epoxies, glues, and resins.
Looking at either product from the perspective of the following factors will allow you to make an informed choice about your type of adhesive bonding solution.
#1: STRENGTH
When it comes to bonding effectiveness, strength is an essential factor to consider. Bonding strength can quickly determine whether an adhesive fails and can fluctuate depending on whether a short-term or long-term solution is needed.
a. LIQUID ADHESIVE
Traditionally, liquid adhesive has been thought to provide a stronger bond than adhesive tape due to its long-term reliability. For instance, epoxies—one of the oldest synthetic adhesive chemistries—have a very high ultimate strength, are resistant to temperature and environmental factors, and, depending on the formulation, have a long shelf life.
Many liquid adhesives are used for structural applications, especially when the load is high and the bond area is small.
b. ADHESIVE TAPE
With adhesive tape, the bond is distributed over the entire adhesion surface. A uniform thickness provides a consistent coverage that also spreads out any physical impacts or bumps, lessening their impact.
Additionally, the backing of some adhesive tape helps balance different degrees of expansion of certain materials in heat or cold, creating strong bonds regardless of high temperatures.
Certain adhesive tapes can match liquid adhesive’s bonding capabilities (one example is 3M™ VHB™ [Very High Bonding] tape), while others don't perform at the same strength level.
#2: CURING
One primary difference between adhesive tape and liquid adhesives is the need for curing. Ordinary glue might require time to dry and harden, but other liquid adhesives, such as epoxy, could require a chemical reaction or other external factors like heat to cure.
a. LIQUID ADHESIVE
Liquid adhesives must dry and harden to form a bond. They are mixed with a solvent, keeping them in liquid form until applied to a surface, when the solvent evaporates. The adhesive then hardens and forms a bond, which can take anywhere from a few seconds to a few hours.
b. ADHESIVE TAPE
Known for being always sticky; adhesive tape holds immediately upon contact. There is no need for a chemical reaction or time for drying. Pressure-sensitive adhesive tapes are always ready to use; just remove the protective liner and apply pressure. However, adhesive tape does require some time to reach its “ultimate strength.”
#3: APPLICATION
Applying liquids can be a very different experience than applying adhesive tape. Depending on the application process you plan, you might accidentally run into serious issues down the road if you’re not properly prepared with suitable adhesive and equipment.
a. LIQUID ADHESIVE
When joining two pieces, you may want to move a piece into place or adjust it. Liquid adhesives are positionable following adhesion because they don't immediately cure, but the application process is messy.
Liquid adhesives may be easier to automate (no liner to remove, no pressure to apply). Still, they require specialized equipment, including an applicator and additional training to get the mixing right. Liquid adhesives can drip, splash, or overflow, resulting in a sticky mess and expensive waste. Lastly, they don’t always consistently cover the bond site.
b. ADHESIVE TAPE
Flexible yet easy to handle, adhesive tape can accelerate the application processes because no drying time is needed. There are no air quality concerns because there’s no poisonous evaporation (some liquid primers expose employees to harsh chemicals).
Adhesive tape has a clean application, and no follow-up work is needed to remove any remains of the adhesive. With die-cut adhesive tape, shapes are cut to the part’s exact dimensions (more on this below).
#4: VERSATILITY
Material versatility can affect its abilities within a single project. For instance, adhesive conductive materials can bond while transferring heat or electricity.
a. LIQUID ADHESIVE
Regarding versatility, many liquid adhesives are conductive and can transfer heat or electricity while maintaining an adhesive bond. Yet, this is the same as adhesive tape, and for many assemblies, either will function. It’s also worth noting that liquid adhesive is not the proper joining method for all joint types.
While liquid adhesives are limited to one adhesive type for two surfaces, adhesive tapes can be laminated with other adhesives to make customized double-sided tape.
b. ADHESIVE TAPE
Adhesive tape can create long-lasting, durable bonds between materials with different surface characteristics. Depending on the materials and adhesive used, it can be bonded to both low-surface-energy (LSE) and high-surface-energy (HSE) substrates.
When temperatures change, a bond of other materials may experience different elongations. Over time, static and dynamic forces act on the bond and must be dissipated, which adhesive tape does.
The construction of adhesive tape allows it to be converted. Die-cutting adhesive tape into complex shapes and exact dimensions allows for accurate application and minimizes waste. This provides long-term and reliable bonding, enhances sealing, and dampens vibrations.
As you now know, there are many reasons why you might choose either liquid adhesive or adhesive tape. However, deciding between liquid or tape is only the first step of your material selection process.
If you’re interested in finding a low-profile adhesive to create a high-strength bond, contact a flexible material converter for a consultation on your application. A converter can help with nearly any bonding challenge by determining the best adhesive tape and sourcing suitable materials.
Reach out for a quote and begin developing your custom solution alongside experts or continue learning about adhesive bonding in our Learning Center.
Originally published: May 20, 2021
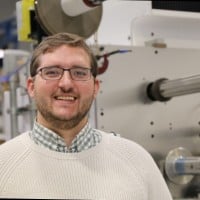