When was the last time you used double sided tape? You’d likely be surprised by what it can do for new products.
Like many great inventors, you may have fallen into the design rabbit hole in search of the material that will guarantee you the best performance. However, how can you choose the right type of double sided tape until you’ve learned how it works and what the different types are?
Strouse has spent over thirty-eight years offering prototyping and production expertise to support new products. Today, we’ll discuss thin bonding and double sided tape variations to help you understand what to expect before entering production.
What is Thin Bonding?
Thin bonding refers to using double sided tape to create virtually invisible, high-strength bonds in different industries.
So, what applications are right for thin bonding? This list could get huge, but these should provide a good idea of its uses:
- Medical devices
- Auto interiors
- Consumer appliances and electronics
- Construction equipment
- Industrial machinery
- Marine parts
- Stick-to-skin
- Signage/Graphics
- Sporting equipment, and many more!
THE ADVANTAGES OF THIN BONDING
Now that you know a few examples of thin bonding solutions, let's discuss why you might use them.
- Design: the lowkey appearance and custom shapes of the tape will enhance your designs
- Strength: thin bonding materials create high-performance solutions
- Production flexibility: allows you to leave the liner in place until the second substrate is ready
- Exact bonding: from low-tack to permanent bonding
Of course, there may also be other advantages depending on the chosen material, such as:
- Soundproofing: some tapes reduce vibration
- Water-resistance: resists contact with water or other liquids; possible submersion
- Temperature: performs in a certain environment, from -40°F up to 200°F
- UV light: resists ultraviolet rays (natural and artificial)
Thin Bonding Variations
1. ADHESIVE TRANSFER TAPE
Adhesive transfer tapes are typically ultra-thin pressure-sensitive adhesive (PSA) tapes without a carrier. They’re engineered to streamline product designs (thinner = less bulk) and make manufacturing easy.
In addition to being the thinnest bond achievable (boosting design aesthetics), the main advantage of adhesive transfer tapes is their flexibility. For instance, circuit boards require flexible tape, and high-end graphics need to be applied without bubbles or wrinkles.
Converters transform these tapes into components that meet the exact specifications of a design, but that’s not exactly easy. To handle transfer tapes’ low tension during converting, expert engineering— the earlier used in the project, the better— is vital to reducing manufacturing issues.
2. DOUBLE COATED TAPES
As stated earlier, the structure is the main differentiator for double coated products.
The critical component is the carrier, which can range from a 3 mil PT to a non-woven scrim (fabric), depending on how much stability the tape is expected to add. The stability of double coated products also makes them more converter-friendly, allowing us to use manufacturing processes without as many limitations as adhesive transfer products.
As more industries use low-surface-energy plastics, adhesives must work without needing flame, corona, or solvent treatment, so 3M developed 300LSE adhesives specifically for those substrates. Similarly, acrylic foam tape is lightweight, 10x stronger than rivets, easy to apply, and not messy; 3M’s VHB tape is a classic example (3M thin bonding tape is well-known for its applications in various industries).
3. DIFFERENTIALS
Differentials are a type of double coated adhesive that generally bonds dissimilar substrates. As we learned earlier, they may require different adhesives on each side to match the surface energy of different substrates.
Differentials could mean bonding the same substrates together, but the adhesive must release from one side more easily to render it usable.
The bond must be stronger on one substrate so that every time the adhesive pulls off, it comes off one selected substrate and not the other. For instance, a wearable medical device adhesive must let go of a patient’s skin and stay with the device when it’s taken off and thrown away.
While you can find stock differential adhesives, the choices are often limited. A high-end adhesive tape converter will create a custom solution if needed. For example, you can combine two adhesives that perform well on two different substrates (along with a carrier in the middle) to create the perfect differential for a particular solution.
What Allows Thin Bonding Tape to Stick?
To understand thin bonding tape, you must learn how substrates' surface energy— both low and high surface energy— is critical to adhesion.
Let’s step back and define surface energy. Adhesion is determined by the molecular force of attraction between materials. How strong that attraction is depends on the substrates’ surface energy. High surface energy = powerful molecular attraction. Low surface energy = weak attraction.
Metal, glass, nylon, polyester, epoxy paint, and rigid PVC are high-surface-energy substrates. Powders and coatings, composites, acetal, polystyrene, PVA, polyethylene, polypropylene, and other plastics are examples of low-surface-energy substrates.
If you remember one thing about surface energy, it should be this: microscopic-level features make a huge difference, and adhesives need to be selected to match each specific substrate.
How to Choose a Thin Bonding Material
With so many different substrates that could be bonded and so many surface energy possibilities, it’s no surprise that there are thousands of types of thin bonding tape. Ultimately, your solution's substrate (object surface), application, and format will determine your chosen material.
- The object you’re bonding determines how to bond it
- You must consider not only the substrate but also its composition and physical shape
- The environment in which this solution will be used must be considered; temperature and moisture are the two most important factors.
- You must know the type of bond required: a permanent or removable bond. Some tapes that could be permanent on a high-energy surface might be perfect removable tapes on a low-energy surface
- Is adding stability to the solution part of the adhesive’s purpose? If so, a double coated tape is likely the answer because it has a carrier in the middle
- The most common, easily recognizable format is using tape from a roll, yet many applications require thin bonding solutions of a specific size and shape
“Simple” bonding isn’t always so simple—that’s why the guidance of an experienced converter is invaluable.
A converter helps determine specific adhesives (and carriers if it’s double coated) for each product and the precise format needed for that application. Tapes are converted and supplied as rolls or sheets, configured depending on the application (machine-applied or manually applied).
If you’re interested in pursuing a thin bonding solution, consider reaching out to get started. Building custom parts is often a complex process, so the sooner you reach out for expertise with your design/drawing, the quicker we can help you with thin bonding.
If you’re new to adhesive tape converting and would like to learn more, you can also check out our Learning Center.
Originally published: February 10, 2021
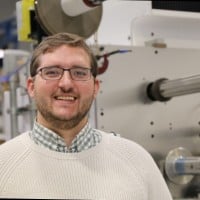