Have you ever mounted something on the wall only to think, “Oh man, I hope this doesn’t fall and scare me in the middle of the night?”
Double sided tape is all around us, from mounted coat hangers on the walls to an EV battery’s interconnected high-temperature inner modules. As a company that manufactures double sided parts daily, Strouse has reviewed countless designs for double sided tape solutions.
Before exploring the many purposes this thin bonding solution may fulfill, it’s crucial to understand how a double sided tape is made. We will review the anatomy, how it's used, and the pros and cons of choosing it.
How Does Double Sided Tape Work?
Double sided tape bonds two (similar or different) substrates (or parts). It consists of two pressure sensitive adhesives (PSAs) on either side of a tape carrier.
A double sided tape carrier is the material that separates and holds the two adhesives, one on each side. The carrier can be made of paper, tissue, plastic, film, or foam material, and its thickness can range from a fraction of a millimeter to a thick foam.
The carrier’s material and thickness are essential for the application the tape must withstand. The stresses an adhesive will be under largely determine the carrier stability needed.
The carrier may have the same adhesive on both sides or a different adhesive on each side for adhering to dissimilar materials with varying bonding properties. As you’ll see below, a release liner is applied atop one or both sides after the adhesives are applied to the carrier. The liner protects the adhesive from exposure until the tape is ready to be used.
The double sided tape shown above is more complex than adhesive transfer tape, composed of a thin adhesive film with a liner on top.
What is Double Sided Tape Used For?
Now that you know how they’re made, what can double sided tapes do? Well, just about anything. You can use double sided tape for hanging, mounting, sealing, gasketing, or other adhesive bonding solutions.
Remember, many bonding applications perform multiple tasks. For instance, a gasket performs a unique sealing function in addition to bonding and succeeds at both when properly designed.
ADVANTAGES AND DISADVANTAGES OF DOUBLE SIDED TAPE
The functionality of individual tapes varies, but generally, many double sided tapes have these challenges and benefits:
Advantages
• Fast assembly
• Design flexibility and clean aesthetics
• Handling strength
• Moisture resistant
• Bond dissimilar and LSE materials
Disadvantages
• Limited use based on the temperature resistance of the carrier
• Conformability is reduced due to the carrier
• Limited conductivity for thermal management applications
Another considerable advantage mentioned earlier is stability. The adhesive’s purpose is often to add stability, so having the carrier in the middle is perfect.
One double sided application is within membrane switches: touch panels that must withstand thousands of flexes, need a certain level of light to pass through, and must withstand high-temperature swings. Having a spacer between the object being touched and the object receiving the signal is integral to their performance.
Lastly, you can customize double sided tape with different adhesives on either side of the carrier, making it into what’s known as differential tape.
WHAT IS “DIFFERENTIAL” IN THIN BONDING?
Differentials are a type of double coated tape designed to bond unlike substrates together, requiring different adhesives on each side.
For instance, a differential tape might join plastic and metal, which stick better to different adhesives. Therefore, it might use two adhesives to achieve the best possible bond with either material.
However, differentials can also bond the same substrate using different adhesives to provide different release points. In certain instances, one side of an adhesive must detach more quickly than the other or release in a particular manner, and differential tapes can achieve this effect.
A limited number of differential adhesives are available in stock, so custom solutions must be created by a high-end converter. For example, a particular solution may require combining two adhesives on a carrier to adhere two different surfaces.
Of the two main thin bonding types — double sided tape and adhesive transfer tape — double sided tape is the most converter-friendly, allowing for many manufacturing processes with few limitations. A carrier provides stability, making the tape easier to handle and convert into small shapes and parts.
What Are My Double Sided Tape Options?
The adhesives on a double sided tape are selected to meet the bonding requirements of different substrates and how they perform; low-tack allows the tape to be easily repositioned, permanent bonding solutions are meant to never release, and there are adhesives for everything between those two extremes.
There are three main types of adhesive chemistries used on double sided tape: acrylic, rubber, and silicone.
Depending on the substrate or surface to which you’re applying the tape, you’ll want to find a double sided tape with enough adhesive strength for your intended purpose.
If you’re unsure which adhesive to use on your material, consider discussing your design with a manufacturer to determine the best option for your project.
Where Can I Find a Double Sided Tape Manufacturer?
Think about how many substrates there are, and it’s no surprise to hear that there are thousands of types of double sided bonding tape. Sure, some tapes can be used straight off the roll, but some applications need a precise size or shape.
It takes expert engineering to reduce manufacturing issues and create a reliable, consistent double sided tape.
An experienced converter customizes double sided tape to perform within the final design, and converted tapes are configured for machine or manual application to match the product’s intended use.
If you’re looking for custom double sided tape, you’ll want to find the right converter. Before you start working with them, consider the questions a potential converter should ask about your project.
For more information about your potential adhesive materials, consider checking out our Learning Center.
Originally published: February 24, 2021
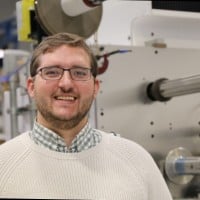