“Hey, we think this tape might work.”
“Great! Let’s invest a million dollars.”
If you’re making important financial decisions for your business, you’ll want to prove the functionality of your design and materials. In fact, proving out a design before full production can save you thousands of dollars in costly adjustments.
Take it from us. As a flexible material converting company with over three decades of experience, Strouse has the experts and the sample-making expertise to understand the ins and outs of pursuing a new product.
Today, you’ll learn how our sample-making process operates so you can decide whether it fits your current goals and also learn the benefits of testing prototypes rather than just material.
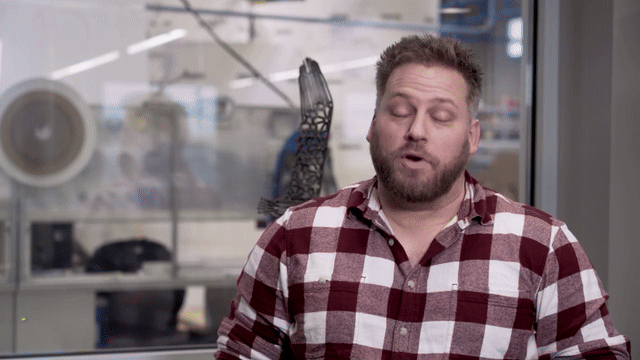
What is Sample Express, and Who is it Intended For?
Sample Express is where our engineers build part prototypes, enabling you to do your testing and adjust your design. It’s a tool to test for design issues, verify engineering suggestions, and prove concepts.
Here are a couple of common reasons why you might consider Sample Express:
- You’re looking for design prototypes
- You’re experimenting with different materials, measurements, or tolerances
Before you request prototypes, you should know that Sample Express is intended to be an additional step in your manufacturing process and ultimately lead to scaling up your process.
While there is technically no minimum order quantity when it comes to flexible material converting, Sample Express might not be the service for someone looking for a one-time handful of parts.
Alternatively, suppose you’ve already done your design testing and hope to produce hundreds or thousands of parts immediately. In that case, Strouse may recommend a die cut trial, which includes costs for material and production time, depending on the quantity.
How Does the Sample-Making Process Work?
The sample-making process begins with your drawing, which you can submit through the Sample Express.
Afterward, Strouse will reach out for details and any additional information that helps us understand the part application to offer the best possible solution. Once you’ve finished discussing follow-up information, it’ll be time to build and ship your part.
FOLLOW-UP INFORMATION
If you’re tired of filling out forms, you might wonder why we need to ask for more information (especially once you’ve already submitted a part drawing).
First, this follow-up info will ensure you include any necessary measurements and tolerances in your drawing so that we can build it accurately.
Second, any additional context you can provide about your project and its intended environment and application will let us verify that the samples we send will function correctly in the circumstances they’re used.
Over the years, we’ve found that knowing more about our client’s projects helps us give relevant material or design suggestions to lower the overall cost and make the part more usable.
BUILDING A PART
Building your part begins with inspecting your drawing and material selection to determine the ideal method for making your sample and potentially scaling up to a large production.
Strouse typically creates samples by laser die cutting or digital knife because they lend themselves to rapid prototyping. Most samples are created using laser cutting and hand lamination, but some limitations exist.
Laser die cutting isn’t always the best choice for high quantities, and delivering laser cut samples in roll form is challenging. If you need an extremely high quantity of part samples, or you need them in roll form, we can discuss your options.
How Long Will It Take to Receive My Samples?
When everything runs smoothly, your sample parts should be completed in 48 hours or less. Yet, the samples are sometimes delayed up to a couple of weeks depending on two factors:
- Do we already have this material?
- Have you shared the crucial part dimensions and material specifications we need?
Material lead time is the biggest time driver because it will take time to acquire if we don’t have it already. The lead time might also depend on our supplier’s sample material availability for each specific material, which has the off chance of being delayed.
Also, without the right part dimensions and tolerances, it’ll be impossible to construct an accurate part based on your needs. Lack of material or proper specifications could cause delays in your sample order.
Should I Request a Sample from Strouse?
Testing rolls of material is different from testing prototypes, which could lead to costly mistakes such as usability issues later on.
For example, if you were building an intricate gasket, you’d want to see how well the material functioned in the intended size and shape of your part design rather than use strips of tape to make guesses.
Before you order a sample, ask yourself whether you’re searching for a flexible material supplier or a converter.
While suppliers ultimately aim to sell the material, converters are trying to prove out a part design that will one day lead to full-scale production.
Suppliers recommend certain materials based on the specifications you put in front of them. However, a converter will use those specifications and your design to build finished products for further testing.
If you’re ready to put your design to the test or check your material selection, consider submitting a request for samples. We’ll contact you shortly after receiving your sample request to discuss the details.
Lastly, as always, feel free to check our Learning Center for more information on project design and material converting.
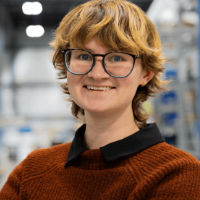