Picture the part you want inside your head. Now, think to yourself, how perfect do I need those measurements?
While converters try to meet the exact dimensions of your part, all die cut parts undergo slight variation. Part tolerances define the acceptable range of variation for each dimension.
With over 39 years of experience helping build custom parts, Strouse’s engineers encourage our customers to test their functional tolerances before defining them in a drawing.
This article will help you understand how to define your die cut tolerances properly and achieve the most cost-efficient and effective outcomes.
Defining a Part’s Tolerances
Regardless if you’re in the prototyping stage or full-scale production, there may come a time when it’s necessary to evaluate your part’s design tolerances. The best way to do this is to define what we refer to as your “functional tolerances.”
TITLE BLOCK vs. FUNCTIONAL TOLERANCES
- Title block tolerances are default measurements included in every part drawing, usually carried over on the template.
- Functional tolerances are the measurement ranges that your production actually requires to function.
The most common (and costly) mistake new product developers make is assuming that their default “title block tolerances” are the best choice for manufacturing. Functional tolerances allow your converter to adjust their methods to avoid unusable parts and unnecessary costs.
Another issue is that title block tolerances can be saved over from a process that is completely different from flexible material converting. Tolerances for CNC manufacturing are not the same as converting. For a converter to attempt to hold CNC tolerances, it would require a significant investment in tooling and automation that might not be justified for that particular application.
If we went by the title block tolerances, you might be looking at tooling costs of $50k+. However, functional tolerances allow you to spend significantly less on tooling costs. This is why you’ll always want to list your functional tolerances instead of sending in the default (title block) ones.
TOLERANCES IN MACHINE AUTOMATION
If you plan on using automation, be aware that your machines' die cut tolerances will likely need to be tighter and, therefore, more expensive.
Die cut adhesive parts applied by hand won’t require the precision that a machine will to register each part and align it automatically. A hand-applied label doesn’t need the same high budget for machine precision tolerances as a die cut part that must be read by sensors before the machine can use it.
How To Set Manufacturable Tolerances
Taking preemptive steps before full-swing production makes die cut tolerances easier to define, thus speeding up the converting process and saving money. The order of these steps isn't set in stone as long as you complete all of them.
#1: DEFINE WHAT THE PART NEEDS TO DO
In order to set manufacturable tolerances, you will first need to define your part's purpose and function. Above all else, this will guide and determine the tightness of your tolerances and the relationship between part layers.
#2: DEFINE THE OVERALL SHAPE
By the "overall shape" of your product, we're referring to the elements or features that need to be in alignment for it to function properly. If a multi-layered product has features that should align, then you'll want to set your overall tolerances tight enough to ensure that you've accounted for the +/- variance that could make or break your part's usability.
#3: SELECT THE RIGHT MATERIAL
Materials behave differently on a die cut press. It’s possible that using stretchy materials, like spandex or foam, will make it more challenging for a converter to achieve proper tolerances.
Stretchy materials extend as they run through the press and snap back to their original form. This can ruin your tolerances and render certain parts unusable. Many materials are also heat sensitive and will expand or shrink depending on their environment, which will also skew tolerances.
Although cutting complex materials is generally possible, it’s better to talk to your converter and check your options before committing to an unnecessarily challenging material.
#4: DETERMINE YOUR FUNCTIONAL TOLERANCES
Let’s say your part had a very precise hole in the center to allow the part to fulfill its function. This would be crucial to specify in your functional tolerances, which would define the range of measurements your process needed the part to hit to pass quality inspection consistently.
One guaranteed way to ensure you’re using functional tolerances is to build prototypes at the higher and lower ends of your tolerances and test them to determine whether they still function. In a product stack-up, this might mean building variations of parts with different tolerances and ensuring that the critical design elements are in alignment.
You’ll want to ensure that all of the tolerances you list in a technical drawing are necessary and specify which tolerances matter to your part function. This will help you avoid over-tolerancing that could complicate your production process and inflate the price significantly. Parts applied by hand often don’t need tight tolerances to fulfill their intended purpose. For example, let’s say you need a label printed for the back of a box, but it’s applied by hand: surely no one will fret over a tenth-of-an-inch margin when the labels are stuck on imprecisely.
Tighter tolerances are more expensive because the tooling cost increases as the part becomes more complicated.
Each die cut tool is custom-made and more challenging to make if it includes odd curves or angles. Tighter tolerances can also necessitate running the process at a slower speed. If you run one million parts in a year, a $5,000 tool could be well worth your while, but it might not be worth the cash for only ten thousand yearly. However, although tight tolerances are more expensive, specific jobs need them. Think about a vinyl border for the screen of a diabetes monitor: any slight misalignment could obscure the data.
Additional Tips to be Successful During the Design Phase
COLLABORATE EARLY ON
Reaching out to a converter during your design phase can be a tremendous asset to the project. If you’re at a flexible point in your part’s design, your converter can offer guidance to ensure it runs well on a die cut press. Designs that lend themselves to converting will transition more easily to press production, which leads to fewer defective parts and an easier set-up process.
INVITE THE RIGHT PARTIES TO THE CONVERSATION
Understand that your converter will likely have technical questions about how your die cut tolerances translate onto a tool, and that connecting us with your experts upfront will eliminate the stress of relaying critical technical information about your part.
Working With a Converter to Define Your Die Cut Tolerances
Now that we’ve established that you can reduce production costs by establishing functional tolerances during your design phase, how do you ensure your design’s manufacturability?
When planning and building your manufacturing process, an experienced converter will consider your design tolerances, material choice, and intended application.
Request a product sample today to test your tolerances. When you request a sample, Strouse’s engineers will also help optimize your drawing for future production processes.
Of course, you may not always be ready for samples, especially in the middle of your design phase. In that case, feel free to still contact us for additional support or read our guide on the cost of tight tolerances as you transition into the material selection and prototyping phase.
Originally published: December 9, 2022
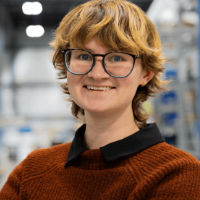