Have you ever been unable to peel a sticker off the sheet? Adhesive release liners are all around you, but people take notice only when they start to malfunction.
Release liners can be crucial to a product’s functionality. Whether cutting, adding, or stripping adhesive liners away, Strouse constantly tests and adapts them so that they fit into your application process.
If you need a release liner, you’ll benefit from learning about the different types and how to choose a liner for an application so you can achieve the best results.
What Are Adhesive Release Liners Used For?
Pressure-sensitive adhesive tape typically consists of three parts: the carrier (or backing), adhesive, and release liner.
The carrier (which doesn’t exist in transfer tape) is a stiffer material that helps the tape maintain its stability and structure. The adhesive layer helps the tape create bonds. PSA release liners, which are coated paper or film, hold sticky adhesive and serve as a protective covering until the pressure-sensitive adhesive is needed. You probably know them as the shiny paper carrying a sticker or label.
In many cases, the release liner is one of the most critical decisions when designing a PSA. It has to have the right qualities and features to precisely match the application (hand-applied or automatic dispensing) and processing (slitting, die-cutting, etc.). Luckily, you have a LOT of options to pick from.
Types of Release Liners
A liner’s base might be paper, polycoated paper, film, or metalized film. It can also be coated with silicone or non-silicone to ease separation from the adhesive. The customization of your liner depends on the precise delivery or dispensing system needed for the application.
1. PAPER RELEASE LINERS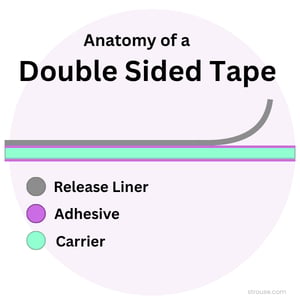
The most common release liner is paper, which manufacturers offer in four main types:
- Kraft (DK)
- Extended densified kraft (XL)
- Polycoated kraft (PCK)
- Extensible polycoated kraft (EK)
This wide range of liners is conducive to creating customized production processes.
2. FILM RELEASE LINERS
Film release liners are steadily increasing, especially for labels and tapes, industrial (roofing shingles, insulation products), and medical/hygiene (electrodes, wound dressings, diapers, etc.).
Film liners generally have two types:
- Polyester (PET)
- High-Density Polyethylene (HDPE)
3. SPECIALTY LINERS
These liners include specialized film (such as metalized film) and other unique substrates for highly specialized applications in various industries (aerospace, automotive, wind energy, etc.).
Manufacturers coat liners with a release agent (often silicone, but not always) to laminate and protect the adhesive from exposure before use. The “release level” is the degree of separation of the adhesive from the substrate, ultimately dictating the liner's characteristics.
How to Match a Release Liner to the Application
Adhesive tape release liners come in different formats:
- Easy, medium, or tight release
- Single- or double-sided release
- Printed
- Medical grade
- Extended liner for easy removal
- Split back
And other adhesive features to fit a wide variety of use cases. Pairing your custom-converted adhesive part with the optimal liner is crucial, especially for automatic assembly processes.
For example, let’s say a print company is preparing inkjet cartridges. The liner’s performance dictates whether the components can be released from the liner as intended during the automated process and dispensed onto the cartridge accurately.
To choose the right release liner, you should provide your manufacturer or converter with information about your application or assembly process. Understanding your needs earlier on will allow them to help you plan ahead and test your part performance with different strength liners.
Finding the Best Release Liner
Choosing the right adhesive release liner will ensure a quick and easy application, but how can you guarantee a good selection for your needs?
By coordinating with your contract manufacturer, you can test out different liners on your custom design. Many converters offer sampling and prototyping services that allow you to test the part before you invest in full-scale production.
Whether you’re in the early stages of material research or already on your way to purchasing release liners, Strouse can help you test different materials and liners until we find the best combination for your design.
Our engineers pride themselves on handling different types of material and investing in your product throughout development. When you submit your part drawing, our engineers will ask about the application and evaluate it for manufacturability. From there, they may test different combinations of materials and liners to ensure your choice is the right one for your project.
Submit your drawing to our Sample Express program today, and we’ll work on creating rapid samples to help solidify your design.
Lastly, see our Learning Center for more product selection and custom manufacturing information.
Originally published: September 30, 2020
.jpeg?width=290&name=0%20(1).jpeg)