What do you think is the most important aspect of automation in manufacturing?
You could argue that it’s locating the best automated machine to maximize your assembly process, but automation starts long before the actual machine purchase.
At Strouse, we understand the importance of planning your automation goals and continuously working towards that acceptance criteria as you begin automation, either from scratch or by transitioning from manual manufacturing.
Creating a rigorous plan for your automation will prepare you to enter the process, but how can you make effective plans without knowing the potential pitfalls you should avoid?
By reviewing the mistakes we see most often in automated manufacturing, you’ll be able to evaluate where you’re currently at, who you’re working with, and what your next steps are moving forward as you continue to integrate automation with your current planning process.
Common Mistakes You’re Making in Automated Manufacturing
Automated manufacturing starts at a different point on each business’s timeline, and while certain companies may plan for automation from the beginning, many companies choose manual manufacturing until their budget and demand drive them to consider automation.
Switching from manual to automated assembly can be a complex feat that requires significant planning. If your product began on an assembly line before reaching the point of automated manufacturing, it’s essential to concentrate your efforts on the transition period between manual and automated applications.
Reaching the point where you can implement automated manufacturing is a massive accomplishment, yet, you’ll want to prepare yourself before diving in.
You’ll learn the most common mistakes in automated manufacturing, the consequences of making manufacturing decisions without prior planning, and how to avoid any additional mistakes involved in automating.
MISTAKE #1: DESIGNS LACK REGARD FOR AUTOMATION
Designing a part for manual application varies from designing one for automation.
Converters consider numerous factors like material, tolerances, and ease of release when designing for automation. Switching from one to the other can be long and arduous without taking steps in preparation.
In automation, part consistency is the key to enabling proper machine placement. When you begin to automate, your die cut tolerances become tighter and far more critical because the spacing between parts is often exact.
Advanced automated machines have sensors that detect parts and re-position themselves to grab them. In contrast, tolerance errors may cause less advanced machines to place parts incorrectly or miss them entirely, leading to lost run time and additional labor through automatic shutdowns.
Your automated process also might require a material with a different liner to ensure the proper release strength. It’s common for businesses to request converters unwind the liner of an existing material and laminate the roll with an easy-release liner to allow machines to pull away the parts easily.
Lastly, designs created before the switch to automation often include custom die cut features like tabs, which require manual removal later in the process. The existing tabs or liners create unnecessary manual labor you can avoid through prior planning.
MISTAKE #2: YOU’RE USING THE WRONG AUTOMATION EQUIPMENT
Generally, if you’re looking to make your automation process run far more smoothly, you’ll want to hold off on buying an automated machine until consulting with a converter.
Automated machines have different processing capabilities, like limits on material width, tolerances, automatic adjustments, and inspection processes, so purchasing a machine without knowing how your part will turn out is risky.
By buying a machine for automatic placement before meeting with a part manufacturer, you’re setting yourself up for a potentially massive financial loss.
If the machine you buy isn’t sufficient and cannot be adapted to suit the part you require, you’ll have no choice but to buy a second machine that can perform the task you want. Worst case scenario, you might sink thousands of dollars into a failed attempt to buy early and save.
Rather than buying a huge, extravagant machine with many features and designing your part around it, design your ideal part and find a machine that suits the part’s automation.
Unless you’ve discussed the material, delivery, application methods, and potential product scalability with your converter, you’re at risk of buying the wrong machine.
MISTAKE #3: OVERCOMPLICATING THE PROCESS
When starting out with automation, it’s common to have a particular image in mind regarding the look of your process.
It’s essential to remember that the most complex machine might not be the most effective or cost-beneficial for your product. While we can all agree robot arms are cool, it’s an enormous cost benefit to buy a simple placement tool instead.
Having an experienced converter as a partner will help you realize you don’t need the most advanced machine on the market to complete your job and that the level of automation required relies on the complexity of your product assembly.
Based on the amount of labor, the process splits into different levels of automation: manual, semi-automated, and fully automated.
Depending on how your application works and where you are in your approach, you could choose a semi-automated method instead of a fully automated one. Instead of buying an entire machine, this might look like buying a jig for quicker, more efficient applications.
In addition, knowing the full extent of your machine’s capabilities might prevent you from adding unnecessary steps.
Many modern automation systems can detect when a part is missing from a roll and automatically skip over it to the next viable part. If your machine has advanced capabilities, you can perform quality checks with the knowledge of the areas of focus your machine doesn’t cover, like the cleanliness of your final product.
MISTAKE #4: YOU DIDN’T PLAN FOR SCALING
Take a moment to consider the best-case scenario: if everything goes according to plan, what are your expectations regarding product performance?
Planning to scale up your product looks different for every company. Still, it often resembles doing research or surveys on demand, reviewing the market share, and estimating the product growth potential based on your expected audience size.
You’ll also want to consider the following: When you order your parts, do you need them sheeted, in a roll, or bagged?
One of the most overlooked factors in manufacturing is the form in which parts are delivered, but automation turns the delivery format of your part into a deliberate choice.
The delivery format of your parts might change once you start automated manufacturing. For instance, if your converter previously shipped you sheeted parts, it’s worth clarifying whether assembling them in roll form would be challenging.
Consider the following: your part production has previously been built around the knowledge that you’d prefer to receive your final product in a certain format. Changing the setup for a part could be simple or extremely difficult depending on how many changes your converter has to make.
MISTAKE #5: BUDGETING THE WRONG AMOUNT
The decision to switch to automated manufacturing is often volume-based, which depends on the number of orders you receive and the amount of labor you have.
However, automation also has a hefty buy-in fee due to automated machines, meaning you’ll have to budget for the initial machine purchase, set-up, run time, and upkeep.
There’s a significant difference between hiring 3 employees to make 25,000 parts yearly versus hiring 20 employees to make 800,000 parts yearly. If you ask too-few questions in the beginning, it could lead to costly changes later in the process.
If your business is rapidly growing and you see a path toward automation, you can start by planning a budget and learning how to scale up your adhesive.
MISTAKE #6: NOT HAVING THE RIGHT PARTNERS
First and foremost, you’ll want a partner with significant automated manufacturing experience.
Experienced material converters know how to ask the right questions to build a product that functions throughout your assembly process. In addition, they’ll offer suggestions like bringing automation into production to create a one-pass process as a simplified alternative to shipping you the parts to conduct your own assembly.
Interested in learning more about automating your part with a converting partner? Read about real-world scaling examples.
What Should I Know Before Automating the Manufacturing Process?
Before automating your manufacturing process, you should know that it’s essential to have a plan in place for the future as well as a budget for capital investments.
When you choose specific goals you’d like your company to accomplish as you automate your manufacturing, you’re far more prepared to plan a realistic timeline of events. Automation takes time, and if you haven’t even gone into manual processes, know that it might take a substantial amount of time to adjust your design for manufacturability.
It’s also helpful to establish a potential budget due to the buy-in cost of automated machines so you can estimate the initial investment and any further maintenance costs. Maintenance costs are a critical consideration of the budgetary planning process, and it’s worth taking stock of the technical support you have in-house before purchasing a machine.
You probably have much to discuss if you’re looking into automated manufacturing. Consider scheduling a project consultation where we can discuss the exact specifications of the design you’re looking to automate and plan how to achieve your production goals.
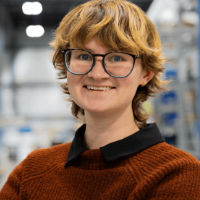