It’s been a minute of staring through the screen of a video call, but you’re still stumped. Why does the flexible material converter need to laminate your material?
Industrial lamination isn’t the same lamination you’d see in an office. Manufacturers use adhesives to bond liners and materials to create custom stack-ups with beneficial properties for your particular application.
Strouse builds laminated parts daily, so we understand how challenging it is to design and produce precision-laminated parts. Laminating is a critical skill for flexible material converting, and we will discuss how its success relies upon a converter’s ability to innovate the process.
You’ll learn what it means to laminate adhesive, why laminating is applicable in converting, and problems that could potentially arise in production.
What Does it Mean to Laminate Adhesives?
Laminating adhesive is the process of pressing two or more materials together to create a new material. It allows converters to create a material that addresses specific application requirements when materials off the shelf don’t address your needs.
Many people think of paper documents when it comes to lamination. However, various flexible materials can be laminated together regardless of composition. Every liner, adhesive, and film has individual properties and characteristics. Lamination can pair adhesives with different liners to create the exact release and stability needed for a product.
Through adhesive bonding and lamination, liners are stripped away from existing adhesive rolls, enabling converters to mix and match liners and materials to create a roll that best fits the application.
For example, modern manufacturers often use automated means of production, but their machines struggle to remove tight-release liners. As a result, they reach out to converters with existing rolls of product and ask us to unwind the material to switch to an easy-release liner.
Another instance of a laminating application is when you cannot locate proper, specialized adhesives to attach two different surfaces on the market.
Using a single type of adhesive won’t be practical for every situation. You might need a differential double coated tape (a double sided tape with different adhesives on either side).
Painted metal has a lower surface energy than unpainted metal, meaning it’ll be more effective with a different adhesive. With the help of a converter, you might laminate a double sided tape to function well on both surfaces and create the ideal bonding solution.
Manufacturers align laminating adhesives with different materials and activate the adhesive bond using pressure to create unique combinations of liners and materials for specific applications.
How Does Adhesive Lamination Work?
Lamination is merging one flexible material with another by applying pressure or heat.
Manufacturing facilities also use rollers to apply pressure when laminating materials, but because most adhesive materials come in rolls, the laminating process becomes a continuous cycle.
Rather than having to stop and switch out parts, converters run the rolls of material through the press to create a steady stream of laminated parts.
WHAT IS WEB LAMINATION?
There are subcategories depending on the type of lamination you choose. For instance, we use web laminating to combine rolled materials at Strouse. If you’ve seen a rotary die cut machine before, you may have witnessed web laminating without realizing it.
Web laminating is accomplished using rotary tools that thread two lines of material through the press and regurgitate them as a single line of adhesive material.
Web laminating includes:
- Multi-layer lamination
- Extended liner laminating
- Liner substitutions
- Zoned adhesive lamination
and is frequently implemented by flexible material converters laminating foams, films, liners, or other substrates using pressure sensitive adhesives.
Incorporating lamination into the die cutting process encourages flexible material converters to aim for a one-pass press run. Ideally, the material goes in on one side and comes out the other end as fully-finished parts.
HOW CAN LAMINATING ADHESIVE GO WRONG?
Earlier, we claimed that success in lamination relies upon a converter’s innovation ability. To be honest, due to the many problems that might arise, laminating complex designs can quickly become a challenge that hinges on engineering ability.
Running a laminating adhesive requires a thorough understanding of how to maintain the correct tension and angles. A flexible material converter can achieve total machine press alignment with the correct angles and a seamless, one-pass process.
1. Using the wrong tension and angles will cause malalignment, resulting in faulty parts with air bubbles that pop or tear and other deformities.- For this reason, converters test their machines before fully running a product and make calculated adjustments for better accuracy.
- Although laminating silicone adhesive with a silicone release liner is tempting, any converter would redirect you to a fluorosilicone liner instead to prevent the silicone from gluing itself together.
Consider speaking with a converter before purchasing laminating adhesives. Based on your part’s application, the converters can help source you a material that enhances your design manufacturability.
When Should I Use Adhesive Lamination?
When you can’t find an adhesive that matches the properties of your substrates, or the “parent” (original) liner doesn’t suit your application method, then it’s time to consider adhesive lamination.
Even if you choose difficult-to-laminate material that’s flexible or flimsy, it can probably still be laminated, even if it costs more due to a longer, more complicated labor process.
Although adhesive lamination is used during die cutting processes, converters can also perform adhesive lamination as a standalone process by laminating material or changing liners without a die cut tool on the rotary press. Whether you want laminated material or parts, converters can meet your needs regarding adhesive.
Finally, if you're unsure how lamination will affect the cost of your die cut, ask your converter about pricing and how they plan to laminate adhesive to your final design.
Originally published: May 11, 2023
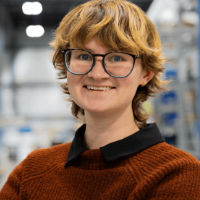