On a rainy Sunday afternoon, I think we can all agree that the most soothing activity is to curl up with a cup of tea andddd— learn whether EPDM suits your gasketing project?
Okay. So maybe finding material is kind of a pain. That’s why we’re going to review everything you should know about EPDM gasketing material.
Having worked with hundreds of flexible materials, Strouse’s engineers are well-versed in the differences in the behaviors between types of rubber for gasketing.
Before you’ve chosen a gasketing material, let’s discuss the properties of EPDM so you can avoid spending excessive money on a part that may not fit your intended project.
What is EPDM?
EPDM, which stands for Ethylene Propylene Diene Monomer, is a synthetic rubber polymer often used for insulation, seals, or gaskets.
When compared to other rubber polymers, EPDM demonstrates a high elasticity and can mimic the physical aspects of natural rubber. Additionally, EPDM has a polyethylene and propylene crystallinity that allows it to possess more elastic properties.
EPDM can endure difficult conditions such as:
- Oxygenation
- Ozone
- Ultraviolet light
- High or low heat
These protections help prevent EPDM from wearing out under pressure, although, due to its highly flexible nature, EPDM isn’t suited for objects that require more rigid or stiff parts.
We encourage you to consider other options if you plan on building gears, shafts, or anything involving structural support.
What is EPDM Resistant To?
Depending on the project you’re working on, you will have different needs when searching for the right gasket material. Here are some factors to consider as you decide whether EPDM meets all the requirements on your checklist.
1. WEATHER CONDITIONS
EPDM gaskets are known for their resistance to ozone and UV light. These two properties are EPDM’s most defining features.
Natural rubber doesn’t have nearly the same protection from the elements as EPDM, meaning it’s more likely to degrade or crack under the harsh glare of direct sunlight.
Even though there are different variations of EPDM rubber, each type is durable enough to withstand outdoor exposure for prolonged periods. EPDM is highly resistant to water, like steam or wastewater, regardless of its temperature and composition.
2. HEAT
EPDM is an excellent choice of material for electrical insulation. Thanks to its ability to survive extreme temperature differences and low conductivity, EPDM is often chosen to build gaskets, wires, cables, and insulators.
- Even in environments full of water vapor, EPDM can withstand temperatures up to 300 degrees Fahrenheit.
- EPDM also remains flexible at temperatures as low as -40 degrees Fahrenheit, which enables its use in freezing weather.
Another widespread use of EPDM material is in roof seams, which stop the outside temperature from creeping in.
Property owners often apply EPDM products to commercial buildings, garages, houses, etc., to cover up blemishes. The material seals cracks together to protect the roof from the elements while resisting sun damage and weathering by any other natural cause.
3. CHEMICALS
EPDM is resistant to many elements and compounds, such as nitrogen, potassium, and sodium. In addition, EPDM is also resistant to the following:
- Mild acids
- Alkalis
- Ketones
- Alcohols
- (Fireproof) Hydraulic fluids
- Detergents
- Caustic cleaners
Unfortunately, despite EPDM’s two primary ingredients being derived from oil and natural gas, its susceptibility to both makes it unsuitable for specific jobs.
Another factor is that the process behind the birth of your chosen EPDM can alter its physical capabilities. Certain variations, like peroxide-cured EPDM, have a better range of working temperatures, but sulfur-cured EPDM is more common and costs less. Nevertheless, peroxide and sulfur-cured EPDM share many of the same advantages, like strong steam resistance.
What is EPDM NOT Resistant To?
As always, with advantages, there must be disadvantages. Here are factors that might dissuade you from using EPDM.
But first, if one or more of these cons apply to your next project, fear not! There are plenty more custom gasket materials, so feel free to reach out if you have any questions or concerns.
HYDROCARBONS
One of the most significant downsides of using EPDM gaskets is their weakness to hydrocarbons, such as:
- Gasoline
- Petroleum
- Oil
- Mineral/synthetic di-ester lubricants
- Grease
- Kerosene
- Halogenated solvents
EPDM gaskets swell up and lose their strength when used in oil applications.
The combination of gasoline/oil/grease weakness can cause EPDM to wear down in parts of aerospace or automotive vehicles quickly, and its general hydrocarbon incompatibility might fail many refrigeration systems.
MELTING
EPDM won’t melt once it crosses a certain temperature threshold. Instead, either nothing happens, or it starts burning.
In other words, unlike their alternatives, EPDM gaskets are NOT flame resistant. Some additives prevent burning; however, this type of cured EPDM costs much more than the alternative.
Benefits of EPDM Gaskets
Instead of having as high of a tensile or tear strength as natural rubber, EPDM is resistant to abrasions and has a robust elastic recovery.
Consider an EPDM gasket if you need a flexible material capable of sealing out fluids. EPDM foam gaskets come in open or closed cell foam, allowing some fluids to pass through the gasket or repel entirely, depending on your need.
- High durability
Their wide temperature range supports thermal expansion and contraction, and they’re also strong regarding outdoor wear. These factors make EPDM gaskets ideal for most outdoor uses, excluding those involving hydrocarbons.
- Elasticity
EPDM’s elasticity also allows for some wiggle room regarding vibrating objects. By definition, gaskets use two static seals to connect unmoving parts. However, EPDM can resume its original shape after its initial flexion.
- Chemical resistance
Because of their high chemical resistance towards alkalis, EPDM gaskets can work well in tangent with liquids such as brake fluid.
- Vibration dampening
There’s also a growing demand for EPDM material in the automotive industry because the barrier it forms against vibration can nullify an engine’s sound.
The value of EPDM gaskets can be high, so it’s essential to carefully consider each factor before deciding on EPDM above other options. Luckily, you don’t need to take a stab in the dark.
Finding EPDM Gaskets
Okay, so you’ve seen the traits associated with EPDM gasket material, and you might be considering it for your design. Now what happens?
Well, if you’re searching for custom parts, you might reach out to an adhesive converter for product samples so that you can test the design before you invest fully in the material.
EPDM gaskets may suit your project perfectly, but why take the risk when you can test one out? Consider reaching out for a sample today, or looking for more gasketing information in our Learning Center.
Originally published: August 9th, 2022
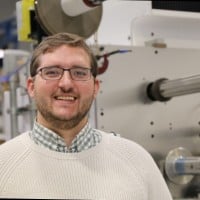