You’ve heard of die cutting, but how do you choose the production method based on your project’s priorities? For example, do you need high precision or high volume? Super speed or complex cuts? Low cost or low maintenance? All of the above??
As a converter, Strouse offers multiple types of die cutting so that you can use the production method that makes the most sense for your project.
If you’re looking to build a product successfully, keep reading to learn about planning the right production method, such as flat bed, rotary or laser die cutting, early on to avoid poor-quality products and wasted expenses.
WHAT IS DIE CUTTING?
Die cutting is a converting process that uses a die tool, usually made of metal, to cut material (paper, plastic, fabric, adhesive, and many more) into identically sized and shaped pieces.
TYPES OF DIE CUTTING
You might be wondering, what’s the difference between rotary, die cut, and flat bed die cutting? How is laser cut different from both of them? Here’s a brief overview of the methods.
- Flatbed die cutting: As its name implies, a hydraulic flatbed press pushes down blades that cut material to the desired shape.
- Rotary die cutting: A cylindrical die, with blades around the entire cylinder, cuts shapes out of the material, moving in a circular motion. This efficient movement cuts out numerous identical shapes as it rotates.
- Laser cutting: Instead of using steel rule die blades to create the desired shape, a laser’s light sears the material. While this isn’t a “die,” it is commonly included in the “die cutting” conversation. The laser easily cuts complex shapes into many materials, yet this process destroys other materials and some adhesives.
The Advantages of Each Die Cutting Method
Like any manufacturing process, the most efficient method is usually the one that best suits the project’s needs.
1. FLATBED DIE CUTTING — Simple Can Be Useful
Flatbed die cutting is arguably the most basic method of die cutting material, and it is the method of choice for many projects.
Flatbed die cutting machines stamp out simple shapes, like a cookie cutter. A cutting die is fabricated and placed in a hydraulic press, which allows it to cut thick material and material in a sheeted form.
Tools can be changed easily and quickly, making flat bed die cutting an excellent choice for low-volume projects or if a product isn’t working correctly on a rotary or laser-cutting machine.
2. ROTARY DIE CUTTING — Best For High-Volume Projects
Think of this method as taking the flat bed cookie cutter approach and then wrapping that cutter around a rolling pin. A rotary die cutting cylinder allows multiple and continuous shapes to be cut quickly from material rolls.
The press’s rotating cylinder blade cuts the material to exact lengths, keeping tight tolerances by using servo motors to maintain registration. Rotary dies, known for their durability, can cut rolls of material that perfectly fit on same-sized objects, which is a critical advantage for parts in the medical, military, and aerospace industries, among others.
3. LASER CUTTING — No Blades Needed
Laser cutting does not require contact with the material. It uses a high-speed laser to perform a variety of cuts. It’s a highly repeatable process that allows tiny details to be cut accurately.
Laser cutting is often used for precision cutting flexible materials (tapes, rubber, laminates) with high tolerance and high accuracy. It’s also a go-to for materials that would otherwise damage traditional die cutting steel.
Flat Bed vs. Rotary vs. Laser Die Cutting
Flat Bed Die Cutting |
Rotary Die Cutting |
Laser Cutting |
|
Speed and High Volume |
- |
✔️ |
- |
High Precision |
- |
- |
✔️ |
Cleanest Possible Cut |
✔️ |
✔️ |
- |
Prototype Friendly |
- |
- |
✔️ |
Clean Air While Cutting |
✔️ |
✔️ |
- |
Deep Cuts or Multi-Layer Cuts |
✔️ |
✔️ |
- |
Material Variation |
✔️ |
✔️ |
- |
Minimize Maintenance |
- |
- |
✔️ |
Do you want to know which is the best die cutting method? Well, let’s compare how each method performs in the most crucial factors:
✅ Speed and High Volume
Flat bed has to index (start and stop) each time it wants to make a cut. A rotary die already has the shape set and can quickly repeat a fixed cut repeatedly. Laser cutting is precise but not fast; it must adjust and follow its cutting shape.
Cutting the same shape across many pieces of material can be challenging, especially if the material is thick. When converting bulk orders quickly, lasers fall short.
***Advantage: Rotary die cutting
✅ High Precision
Laser cutting is fantastic for intricate, complex shapes with tight precision and finishing; rotary and flatbed are limited by how close blades can be placed together.
***Advantage: Laser cutting
✅ Cleanest Possible Cut
Laser cutting doesn’t win here because of laser ablation. The high-intensity laser beam melts or burns a material to get through it, leaving some residue behind, on the edge of the cut.
***Advantage: Rotary die cutting & Flat bed die cutting
✅ Prototype Friendly
When a quick prototype is needed, laser cutting is easier and cheaper than acquiring and using hard tooling. If a high volume is eventually required, an investment in rotary die cutting can be made.
Training on a laser cutter is simple, and operation is easy. Both flat bed and rotary die cutters have more working parts. For instance, the die within a rotary die cutter must be physically replaced after it wears down.
***Advantage: Laser cutting
✅ Clean Air While Cutting
As mentioned, lasers burn/melt materials, which can give off fumes and smoke ranging from inconvenient to harmful, depending on the material. For instance, when PVC is cut with a laser, the byproduct is chlorine gas. Also, smoke can negatively affect the laser’s cutting performance, possibly producing an inconsistent cut.
***Advantage: Rotary die cutting & Flat bed die cutting
✅ Deep Cuts or Multi-Layer Cuts
Generally, laser cutting isn’t effective on thick material or many layers. If you have to do multiple cuts at different times, it will require having multiple lasers, which isn’t always feasible. Having multiple dies, on the other hand, is much more economical.
***Advantage: Rotary die cutting & Flat bed die cutting
✅ Material Variation
Laser cutting is limited by the material being converted more than other methods. It also depends on what type of laser is used to cut. Wavelengths differ, so some materials — conductive material, high-temperature plastics, polycarbonate, etc. — can’t be cut effectively by many lasers.
***Advantage: Rotary die cutting & Flat bed die cutting
✅ Minimize Maintenance
Rotary and flat bed cutters are like other mechanical equipment, requiring refurbishing or replacing when the metal-cutting dies become blunt. Continuous maintenance and potential downtime aren't issues with laser die-cutting.
***Advantage: Laser cutting
Finding the Right Die Cutting Method
As you’ve seen, each die-cutting type has advantages and disadvantages. Deciding which die cutting method to use will ultimately depend on the material you’re using and your ideal quantity.
Most converters count on their die cutting as their bread and butter service. Yet, not all invest in the latest equipment and in-house talent to offer expertise in flat bed, rotary, and laser die cutting.
If you’re ready to begin your project, consider requesting a quote from Strouse. We’ll use our knowledge and experience to plan your production in the most efficient way possible.
Lastly, visit our Learning Center to learn more about adhesive converter's offerings or find out more information on flexible material processing, selection, and quoting.
Originally published: July 8, 2021
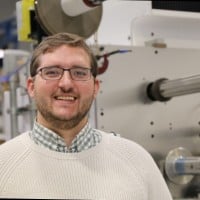