It’s another long day of opening emails and wincing at the sight of material quotes. After taking a break to sip coffee, sigh, and bury your head in your hands, you may begin to wonder how adhesive manufacturers determine their prices.
Or maybe not. Regardless, the answer might help you budget for your projects.
Many different factors contribute to the cost of your materials. As a flexible material converter, Strouse has kept our eye on any climbing industry rates to offer our clients the best deals.
Before you make material purchases, it’s crucial to understand where the costs are coming from and how to get the best value for your orders. This article will inform you about the behind-the-scenes of adhesive manufacturing so you can make better purchasing decisions.
What is Adhesive Manufacturing?
Adhesive manufacturing transforms raw materials like natural or synthetic rubber, acrylic, plastic, chemicals, lumber, or other components into products like rolls of tape, liquid adhesive, liners, and backing materials for further processing or consumer use.
This is not to be confused with adhesive tape converters, who purchase material from adhesive manufacturers and transform it into customer-specified shapes and sizes.
What is an Example of Adhesive Manufacturing?
Companies begin by purchasing and processing raw materials to eliminate impurities and enhance certain desired traits. Once they have processed the raw materials, manufacturers transform them into the final product. Depending on the desired result, an adhesive manufacturer’s final product might look like tubes of glue, pressure-sensitive adhesive tape logs, or another material format.
An example of adhesive manufacturing would be the complete process of making polyethylene tape. Adhesive manufacturers buy and process petrochemicals to make synthetic rubber adhesives for their tapes. Then, they use additional raw materials to manufacture paper and film for adhesive backings and liners.
In the case of polyethylene tape, the adhesive tape manufacturer uses large-scale machines to apply the synthetic rubber adhesive onto a polyethylene backing material and process it into massive tape logs.
Adhesive manufacturers sell tape logs (“jumbo rolls”) to companies that process their own parts and materials. However, they also often sell these materials directly to converters for roll-to-roll processing to build complex products or transform them into smaller rolls that fit their clients’ desired dimensions.
The Cost of Adhesive Manufacturing
Adhesive manufacturing pricing impacts your overall product cost, but it’s based on a combination of factors. Understanding these factors will help you map out pricing from raw materials to the finished product.
RAW MATERIAL PRICING
While some raw material DOES, in fact, grow on trees, this process requires careful planning and processing before it’s in any workable condition.
For instance, certain raw materials, like natural rubber, require time to cultivate. During the pandemic, there was a rapidly increasing demand for natural rubber and other raw materials, which has effects still present in the market today. Rubber trees take 4 to 7 years to produce latex, meaning the planting surge in response to consumer needs still hasn’t entirely caught up to their increased demand.
Adhesive manufacturers either source raw materials from a third party or own a production facility that collects them directly. Natural and synthetic materials often undergo many processes before becoming usable products, requiring additional chemicals.
By adding components like carbon black, adhesive manufacturers can strengthen the durability and adjust the elasticity of raw materials. However, these chemicals are also subject to their own prices, so when the cost of adhesive manufacturing increases, it might be the cost of the additives used to transform raw materials into finished products.
NEW LAWS AND REGULATIONS
As events occur worldwide, staying up-to-date on how material and manufacturing prices are affected is essential. Many updated laws and regulations have affected adhesive manufacturing:
1) Trade sanctions
In response to Russia waging war against Ukraine, many countries have placed restrictions and bans on certain imports and exports, such as crude oil and petroleum products. Places with these restrictions include countries in the E.U. and the United States of America.
Other sanctions have affected the cost of rare minerals and metals like nickel and copper, which are used to produce foil tapes and other components of the adhesive-making process.
2) Increased rubber sourcing regulations
In the past few years, the European Parliament has worked towards tightening supply chain laws to ensure better sourcing practices and reduce harm to people and the environment.
The Supply Chain Sourcing and Obligations Act (SCA) has already had an economic impact on the rubber industry. Yet, we know the requirements are expected to continue evolving.
With concrete new methods to trace rubber sales as a means to guarantee its ethical sourcing, many adhesive manufacturers might need to seek out partnerships with domestic companies.
3) New consumer vehicle regulations
Along with increased regulations regarding the impact of combustion engines, today’s consumers are increasingly aware of environmentally friendly vehicle options.
One of the biggest, rapidly expanding changes to the current consumer market is the expanding demand for electric vehicles. This has led to material experimentation using rarer minerals and other components that might aid in the production, functionality, and safety of EV batteries.
As the market demand shifts, so does the demand for manufacturing with innovative raw materials. Yet, some of these materials are challenging to source, affected by current regulations, and have negative environmental consequences.
Electrical vehicle demand is having ongoing effects on the cost of automotive adhesive components, and this will continue to develop as the clock ticks down toward increased mandates for combustion engines.
What Else Should I Know About Purchasing Adhesives?
Buying from an adhesive manufacturer is a strategic process. When purchasing adhesive material in massive quantities, buying directly from the manufacturer might be the right choice. However, if you’re looking for customized rolls with custom lengths or shapes it won’t make sense to order directly from the manufacturer. This is where distributors and converters come in depending on the project. If you’re looking to buy adhesives and manufacture products, you’ll want to know how to do so in the most cost-effective way possible. This article should help in that decision making process.
Before you buy any type of adhesive tape or flexible material, consider your end goal and whether it makes sense to first reach out and discuss your project with a converter.
Contact an adhesive converter for a quote and learn how optimizing your project plan and reducing the number of machine processes can save you money. To learn more about what a converter can do for you, consider downloading this guide to see our full list of capabilities and additional ways Strouse can help.
Originally published: September 5, 2023
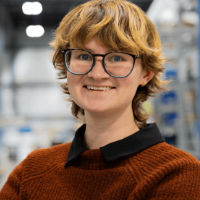