What if you discovered that cutting-edge inventions were transforming the landscape of medical device manufacturing? Your first question would likely be, “Which innovations are leading the way?”
The medical industry is a powerhouse of continuous research and breakthrough inventions. While many inventors keep their projects close to their chests, clear trends are shaping the future of medical device components. Understanding these trends is essential for staying ahead in an industry driven by precision, innovation, and patient care.
As a converter with over 30 years of experience building custom parts, Strouse’s team has helped develop medical device components from prototype to production.
If you work on specialized medical products, this guide will explain up-and-coming technology and its considerations so that you can better understand the development process.
Defining Medical Device Components
Medical devices encompass many healthcare products, from hospital equipment to at-home monitoring tools.
Any feature that contributes to a medical device's functionality can be considered a medical device component, which includes:
-
- Printed circuit boards
- Skin adhesive sensors
- Imaging systems
- Battery cases
- Cable assemblies
And many other parts that manufacturers use to build medical equipment.
Due to the wide range of products, medical manufacturers often outsource specialized components when building devices. Manufacturers and converters can source cost-effective materials and simplify part designs to create efficient processes.
Understanding the different types of components can help you plan your production method (such as rotary die cuts vs. injection mold) and application process. Let’s begin by reviewing a handful of devices.
Trending Medical Devices & Their Components
Each year, new trends become evident as the Food and Drug Administration approves new medical technology. For instance, 30% of FDA-authorized medical devices were classified as Lab Tests in 2024, which is a 7% increase from 2023.
The following list was compiled from FDA data and testimonies from Strouse’s subject matter experts about budding technology. Our goal is to provide insight into current industry trends for anyone interested in designing and manufacturing medical devices.
1. REMOTE MONITORING TECHNOLOGY
Device-based remote monitoring (DRM or telemonitoring) tracks vital signs to provide updates and decrease hospital service use. Remote patient monitoring devices, such as blood flow or EKG monitors, consistently track bodily performance and provide support.
Examples of remote monitoring include:
-
- Cardiovascular monitoring
- Blood pressure / arterial pressure monitoring
- Pulse oximeter
- Continuous glucose monitoring
- Pregnancy monitoring
- Biosensors
- Cardiovascular monitoring
Many remote monitoring devices are attached to the skin using medical-grade adhesives, which can create unique challenges for product design.
DEVICE-TO-SKIN ATTACHMENT ADHESIVES
Attaching a device to the skin requires an adhesive material that can adhere to both the device material and the skin’s surface.
Inventors often encounter issues by using the same adhesive for both the skin and the device when a double-sided differential adhesive is more favorable.
Differential adhesives have a different adhesive on either side of the tape’s carrier. Many differential skin adhesive tapes use a powerful acrylic adhesive on one side for device attachment and a more gentle silicone adhesive on the other for the skin. However, this formula may differ for parts that must remain in place for extended periods.
Long-term skin adhesive products use specialized adhesives to hold heavy devices in place without straining the user’s skin. For instance, transdermal patches designed to deliver drug solutions might be worn for consecutive days, allowing them to seep into the dermis properly.
Experienced manufacturers may recommend using specialized, long-lasting stick-to-skin adhesives like 3M’s 28-day wear-time adhesive, which is intended for sensors and medical wearables.
2. DIAGNOSTIC TESTS
Rapid diagnostic tests, such as PCR tests, can detect infectious diseases like COVID-19 or influenza. Other rapid tests, such as glucose blood metering, measure blood sugar and other biomarkers.
MICROFLUIDIC COMPONENTS
Microfluidic parts are a common diagnostic tool used to provide timely and accurate results. These devices contain tiny channels for liquid to flow through, facilitating tests that are minimally invasive and efficient to perform.
Microfluidic part components can be laser cut or engraved with channels and other features, which is especially useful for small-batch prototyping samples.
3. MOUTH TAPE
“Mouth tape” refers to a product line designed to improve sleep quality and jaw posture. These skin-safe tape products are placed over the mouth to hold the lips together and are sometimes used with CPAP machines.
Mouth tapes are most commonly made using micropore tape. However, with an increasing range of skin-friendly products on the market, some brands have started experimenting with the breathability of their mouth tape material.
Mouth tapes are not the same as oral bandages, yet both are made from flexible materials that can be laminated and die-cut into custom shapes.
4. MEDICAL IMAGING REFERENCE POINTS
Medical imaging tools, such as X-rays, often benefit from some form of radiopaque markers to designate specific areas of the body for image analysis.
One example of a radiopaque marker would be a stick-to-skin adhesive with a radiopaque material lamination or a radiopaque ink coating that shows a high contrast to display bodily sections, draping clips, or other features on a fluoroscope or film. These specialized materials may be pricey, but higher quantity orders can help offset some of the material costs.
5. SURGICAL ADHESIVES
Surgeries are incredibly precise and require clean, well-arranged, and safe spaces for surgeons and patients. Medical-grade surgical adhesives help improve organization and patient safety.
Examples of adhesives used in surgical care include:
-
- Clip holding cables out of the way
- Labels and checklists
- Tapes to secure ties, seals, or surgical drapes
- Surgical equipment prep & management
- Patient protection in/after surgery
These adhesive parts may require sterilization, so you should discuss the material choice with your manufacturer before starting production.
6. MICRONEEDLING DEVICES
Microneedling devices have become increasingly common in the medical industry for pharmaceutical delivery.
Microneedle patches are commonly used to give intradermal injections over a gradual period. They often contain small molecule drugs like antibiotic and antifungal medications or anti-inflammation and anti-scarring drugs. These devices can also contain macromolecule drugs, nucleic acids, and more.
Many microneedle devices are placed onto skin adhesive patches using machine automation, so you may want to find a manufacturer with the experience and capabilities to automate processes and work with skin-safe adhesives.
Developing Your Medical Device Components
Whether or not your intended product was included on the list, each medical device component may have its own unique design, sourcing, and application challenges.
For example, an electronic medical device component may have stringent requirements for the manufacturing environment, such as low-particle and humidity level specifications, which can be achieved in a Clean Room.
It’s possible that you’ve worked with manufacturers who were unable to meet high-quality expectations or provide timely trials for FDA-compliant testing. However, a trustworthy company will meet your expectations while helping guide you through the process.
If you’re interested in working with an experienced converter to build your medical device components, reach out to Strouse for a quote. Our experts will help you locate the most suitable materials for your budget and process and optimize your project for maximum efficiency.
Don’t settle for faulty products made by subpar medical device component manufacturers; submit your part design today. Lastly, you can also check out our Learning Center for more information on medical manufacturing.
Originally published September 12, 2023 — updated since
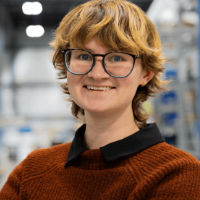