You’re sitting there, head in your hands, trying not to panic about a new printing project. Why all the stress? It’s probably because you haven’t found an in-depth explanation of printing processes that are combined with die cutting services. Stress, begone!
Printing has become a simultaneous step in die cutting for branding, instructions, and warranty information. By combining the two, you can create accurately printed custom products.
At Strouse, our engineers transform client designs into one-pass production processes to reduce the steps needed to build a product. Yet, different factors are involved depending on the type of printing.
Today, we’ll explain how printing functions in die cutting, how it’s automated, and why a converter might suit you.
What is Die Cutting in Printing?
Rotary die cutting is a production method that can be combined with printing to create identical printed components. By integrating printing into the process, you can increase the customizability of a custom die cut design.
Some examples of die cut printed goods include medical products with logos/instructions and industrial packaging labels for item inventory.
DIRECT VS. INDIRECT PRINTING
Direct and indirect printing are two of the most popular modes of industrial printing.
Direct printing is when the printed image is transferred directly to the substrate from the print source. E.x.:
- Flexographic printing (Strouse’s primary print method)
- Gravure printing
- Screen printing
- Lithography
- Letterpress printing
Indirect printing is when the printed image is transferred from the print source to an intermediate surface and then from that intermediate surface to the substrate. e.x.:
- Offset printing
Printing in Die Cut Production
There are many important factors to consider when it comes to deciding how to go about printing a new part in a cost efficient manner. For instance,
- What kind of material are you buying?
- What type of ink will you use?
To better understand printing in production, we’ll first want to look at the different types and decide which one works best for you.
1. FLEXOGRAPHIC PRINTING
Flexographic printing, or “flexo” printing, occurs when ink is loaded into a tray and transferred via a series of engineered rollers to a removable photopolymer print plate. The print plate has raised areas that create the desired print image, which picks up the ink and continuously transfers it directly to the substrate as the material moves under the plate as the entire assembly rotates.
This technology is best suited for high-volume high-speed printing of static, non-variable, simple, images (e.x., Printed Logo Tape).
2. GRAVURE PRINTING
Similar to flexo printing, only the removable photopolymer print plate is replaced by a print cylinder with the desired print image finely etched into it. The ink fills the etched areas as it rotates partially submerged in the ink reservoir, the excess is removed via a doctor blade, and then the printed image is transferred directly to the substrate.
This technology is best suited for high-volume, high-speed printing of static, non-variable images that require finer detail and sharper print (e.x., Magazine Covers).
3. SCREEN PRINTING
Screen, also known as “Silk-Screen” printing, involves forcing ink through an engineered screen, which meters the amount of ink deposited, through a template that controls the shape of the printed image with a wiper blade or squeegee.
This technology is best suited for applications requiring durability, high opacity/thickness, and rich colors (e.x., T-Shirts).
4. LITHOGRAPHY
Lithographic printing utilizes the fact that oil repels water. The printing plate or cylinder is prepared, so water is only received in the non-image areas. Oil-based ink is then applied to the print plate or cylinder via a roller, which is only accepted in the image area. The image is then transferred to the substrate to create the printed image.
This technology is best suited for applications requiring crisp print and high-quality colors. This technology primarily shines as an artistic medium vs. commercial production. The offset version of this printing method (more below) is predominantly used for high-volume production (e.x., Artistic Prints).
5. LETTERPRESS PRINTING
This is a mostly obsolete printing technique in the world of mass manufacturing. In this process, ink is distributed onto the raised surfaces of a flat printing plate, similar to a stamp, which is passed under a cylinder wrapped with the substrate as the cylinder rotates.
This technology is primarily used for artistic/stationary purposes (e.x., Fancy Invitations).
6. OFFSET PRINTING
Offset, also known as “Offset Lithography” printing, is essentially the same process as lithography, but instead of being transferred directly to the substrate, it is transferred to a rubber sheet or cylinder called a “blanket.” The image is then transferred from the rubber blanket to the substrate.
This technology is one of the most widely used printing processes today and, as mentioned above, is best suited for high-volume production with crisp print and high-quality of colors (e.x., Magazines).
7. DIGITAL PRINTING
Digital printing is a very different printing technology because no physical image is transferred through plates or cylinders; the image is created from a digital medium.
INKJET
- Inkjet is a digital printing process that creates images by spraying microscopic ink droplets onto the substrate.
- This technology is ideal for cost-effective short-run printing where vivid colors are required (e.x., Printed Pictures).
LASER
- Laser printing uses laser beams to neutralize negatively charged ions across a rotating drum to create a “negative” of the desired image, these areas of no charge accept the toner particles and are then transferred to the substrate, where they are fused with heat and pressure via a heated roller.
- This technology is ideal for sharp black text and is faster than inkjet, allowing for better turnaround times (e.x., Office/Document printing).
8. THERMAL TRANSFER PRINTING
Thermal transfer printing uses ribbons (though the ribbons are more like adhesive backings than the kind you put in your hair). These wax or resin-coated ribbons contain transferable text that melts onto the target material once heat is applied.
Unlike direct printing, the process of thermal transfer printing is quite long-lasting. For this reason, thermal transfer printed labels are often used for barcodes or clothes tags (e.x., Outdoor/Permanent Labels).
Thermal transfer printing is significantly more costly due to the replaceable ribbon but also enables colorful, weather-resistant graphics. Consider thermal transfer printing to create a label that won’t wear down.
DIRECT THERMAL PRINTING
Direct thermal printing involves a print head that applies heat and pressure directly to the substrate, a specialized material that turns black when heat is applied, to create the printed image (e.x., Short term/Shipping Labels).
Automation In Your Printing Process
One modern invention that increased production efficiency was the ability to guide a fresh die cut directly into the printer. This is typically done by leading the product into a thermal transfer printer, which is then stamped with the proper design and sorted in with the other finished products.
When it comes to automation in printing, you're either guiding die cut parts into a printer or cutting pre-printed material. However, either option could make sense depending on your timeline. Of course, you must also consider printing precision (fixed vs. variable) and customization.
FIXED VS. VARIABLE PRINTING
Variable or “random” printing occurs when working with a set pattern, but the location of the printing isn’t necessarily critical. The printing will be there, but it won’t be in the same spot from part to part.
In variable printing, a millimeter difference doesn’t mean life or death. Therefore, while the parts should still be very close in appearance, they aren’t 100% identical.
Alternatively, the process of fixed printing is much stricter with tolerances, with parts often marked with sensors to line up perfectly. If your product serves a critical purpose or branding is a value-added service, you may need to use fixed printing for the same results every time.
PRINT CUSTOMIZATION
Depending on the field you’re operating in, you may benefit from using serial numbers in your print.
For example, say you have a small number of highly specialized parts to work from. Surely, you want to keep track of each part to ensure it ends up in the right place.
Serial numbers exist to follow specific products to study their performance. If one product has an issue, the manufacturer must contact other batches and check for errors.
We’ve also seen the use of lot numbers and expiration dates, especially in the medical field. This type of traceability is often a firm requirement.
Custom Branding
How is your business seen through the public eye?
As you may already know, branding is curating your company’s reputation. Part of this is through image association, such as your company logo or color scheme.
Your brand colors, logo shape, and many other elements can help you build a strong reputation and recognition.
SPOT COLOR PRINTING
“Spot colors” are the best way to acquire your desired printed color and are essential for product branding.
Different companies have different color schemes, making it necessary to print in the exact color that represents your brand. Yet, most printers run a few different shades of ink and can only create specific colors.
Ordering a specific shade is more expensive than the default options. However, an increased number of manufactured products can justify the pricing difference. Mixing a small batch of custom colors for a handful of parts will cost more in proportion than ordering a larger size.
Don’t sacrifice your brand reputation to find a color that’s close enough. With the right partner, you can strive for perfection every time.
Die Cut Printing and Converters
So, let’s say you’re hoping to find custom die cut printed designs— where can you find them? If you want custom die cutting services, consider a converter.
A converter is like a baker: you can purchase the raw materials yourself, but a converter will deliver you the finished product. If you needed a cake baked, you wouldn’t order it plain and ask a second bakery to frost it.
Why have an object cut and shipped elsewhere for printing when it can all be accomplished in the same place? Converters have the experience to integrate your printing needs into a custom die cutting process to build a more efficient one-pass production.
If you want to know more about what Strouse can do, feel free to look at our printing services above or see our full list of capabilities.
Originally posted: October 7, 2022
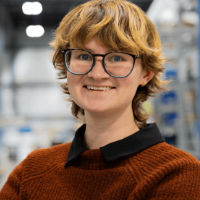