You’ve just purchased your brand new car, and you’re excited to drive off the lot when you notice a huge scratch arcing down the side. The big mistake? A lack of protective film.
Protective film has always been the magic that's brought your sparkling new cars from the manufacturer to the dealer's lot.
For decades, Strouse has been transforming protective film into custom-made pieces to cover vehicles, devices, and more.
Once you’ve read the industry benefits, you’ll understand how protective film helps protect vehicles and other surfaces from the daily wear and tear that comes with regular usage.
What is Protective Film?
Protective film is a material that protects surfaces that are susceptible to damage: minor or moderate abrasions to scratches and more.
Protective films were originally developed with military applications in mind.
Back in the '60s, the U.S Department of Defense realized that their helicopter blades could not escape the damage caused by debris in the air. This problem eventually inspired the creation of a protective layer that was designed to be transparent, lightweight, and strong enough to prevent damage to the military equipment in use.
These protective layers, or “helicopter tape,” evolved into the protective film we see on modern-day vehicles.
Today, we’ll discuss the protective film benefits we’ve seen in industries we’ve worked with and how it could benefit your future projects.
What is Protective Film Made of?
Protective film serves many different purposes and industries, so its composition depends on the part application.
Here are a few specific types of materials, primarily plastic, that are commonly used to create protective film:
- Low-density polythene films have enhanced elasticity and flexibility, and are generally low in weight
- Polyvinyl chloride is sleek with relatively higher levels of elasticity, making it an ideal option for metal surface protection
- Polypropylene is less elastic and holds firm even in higher temperatures
- Polyolefin works exceptionally well with glass or painted metal, and specific variants are used for packaging
- Co-extruded, low-density polythene provides a higher level of protection by using layering techniques
- Paper is generally used to protect against very low-impact damage
Types of Protective Film
Protective film comes in a variety of styles, each specifically designed for an application, and they generally vary according to thickness, material, and adhesive strength.
These are two of the most common types of protective film you’ll encounter:
1. SURFACE PROTECTIVE FILM
A high-quality surface protective film can easily be applied and removed while providing a sleek finish to the surface it is used on. These films protect vulnerable surfaces: glass, commercial glazing, plastic, stone, brick, granite, marble, and more.
Industries with a focus on manufacturing and distribution of packaged products generally find themselves with a need for this kind of protection. However, cutting these films into appropriate shapes to fit various surfaces becomes difficult. Additionally, the user has to ensure minimal bubbling upon application, which often requires a professional’s expertise in surface protection films.
2. PROTECTION FILM FOR PAINTED SURFACES
Paint protection films generally have a higher resistance toward impact. Variants such as the clear paint protection film (PPF) have “self-healing” properties that allow them to return to their natural shape after impact or abrasions.
These kinds of films are usually made from elastomeric polymer, providing elasticity to the film. They’re traditionally invisible, allowing the object to maintain its aesthetic value while adding a level of protection. That’s why common uses include cell phones, electronics, cars, airplanes, and other equipment.
While PPF is not bulletproof, it does provide superior protection against rock chips and other environmental contaminants. It is also chemical resistant, allowing you to wash or clean your equipment without fearing the loss of adhesive or the inability to execute maintenance practices.
What are the Benefits of Using Protective Film in my Industry?
Protective film applications are varied and nearly limitless. However, in the aerospace, electronics, industrial, automotive, medical, and defense industries, protective film can be especially crucial to functionality.
In the following industries, the protective film offers benefits such as protection from scratches and abrasions, shielding against humidity and dirt, resistance against hot or cold temperatures, UV resistance, and chemical resistance.
Flexible material converting is complex! Get your questions answered in this handy Q&A guide.
AEROSPACE
Aerospace engineering constantly strives to create quieter, lighter, and damage-resistant equipment. In the aerospace industry, films are essential for prolonging longevity and enhancing the quality of aircraft materials.
ELECTRONICS
Electronics like mobile phones and other hardware are susceptible to physical damage, particularly screen damage. There is also a wide range of application possibilities for television manufacturing companies, electronic shipment companies, and other similar businesses.
INDUSTRIAL
In general, industries have broad applications for protective film and often require customized protective film pieces to fit equipment or newly manufactured products. End products can suffer plenty of damage on the commutes to distribution centers or warehouses.
AUTOMOTIVE
From wheels and doors to fenders and bumpers, cars need overall protection. Protective films are a fantastic way to achieve general surface protection without compromising the aesthetic appeal of your vehicle.
MEDICAL
Medical devices are usually expensive and require high maintenance to prevent metal corrosion. Adding a protective layer helps prevent premature wear and tear and keeps the machines running smoothly.
DEFENSE
Defense equipment likely requires more intense types of surface protection. Protective films help ensure critical military equipment, weaponry, and machinery run efficiently.
Which Protective Film Should I Choose?
To correctly choose the right kind of film for your needs, you should consider the following elements:
Longevity: Installing cheap film that will spoil within a few months is counter-productive. Instead, invest in a high-quality, branded film that offers durability.
Warranty: Ensure that the product you are investing in has reputable customer care and good deals on warranty. Generally, a Pregis PPF would provide up to ten years of warranty. This is excellent for equipment like cars that you will likely use long-term.
Quality: Now that you're aware of the role material plays in determining the quality of the film, ensure that you ask questions about it. At the very least, you should be able to get PPF that crosses all the basic requirements of being scratch-resistant, abrasion-resistant, and UV protected.
Of course, quality depends on the budget you have, but on the whole, it is relatively easy to get high quality for reasonable prices.
Application: The application or installation of protective film can be challenging, especially when you have no experience. Ideally, you should hire an expert to ensure you avoid bubbles on the surface.
How To Succeed in Using Protective Film
No doubt, the quality of the film material largely determines if it’ll be adequate for the task required. That said, two aspects of protective films are critical to remember.
First, partner with someone who understands material selection — the variety of sizes and degrees of thickness, with some offering multi-layered, stronger protection. The more complex the object, the higher the need for customization, the second vital aspect.
Second, make a plan to execute your project: modern-day advances in rotary die-cutting allow converters to achieve precise results even when dealing with highly specialized aircraft and other intricately designed objects. Protective film application to complex objects requires expertise in working with heat guns, torches, plotters, spray fitting, and other installation techniques.
You may have a vision in mind for how protective film will benefit your particular industry, but you may be wondering what type you should use, or when your part will reach its final design. Using the experience we have working with a wide range of materials, our engineers at Strouse know it’s essential to find the right film and optimize the design for your innovative solution.
If you have a protective film application, your next step could be finding a converter who meets your particular needs. At Strouse, we pride ourselves on being able to deliver highly customized parts that fit the particular needs of your product and application.
See what it’s like to work with us or reach out for a quote today:
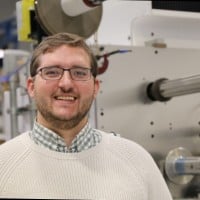