Sheeted stickers. Adhesive wall mounting strips. The split tabs on the backs of band-aids. These inventions stem from a particular production process that increases part usability: kiss cutting.
Kiss cutting is a shallow cutting method that enables engineers to integrate more complexity and functionality into customer solutions while keeping costs low, especially with pressure-sensitive materials. However, it opens the door for numerous potential headaches with defects, and fallout increases when incorrectly performed.
What is Kiss Cutting?
Kiss cutting uses a die tool to cut material, except the tooling is adjusted only to cut the top layer(s) of laminate, leaving the liner, backing, or remaining layers untouched. Kiss cutting is a type of die cutting, but die cutting also includes through cuts.
The name originates from the idea of a blade cutting through one material but barely touching the second. This can leave a slight imprint, but the second layer should remain unpenetrated. It can be performed on a rotary, flat bed, or laser machine press.
The tan laminate is a backing of the black double-sided adhesive in the image pictured above. A through cut would slice through the black adhesive and its backing, whereas a kiss cut would halt after the first cut without damaging the tan layer underneath.
For instance, the kiss cut area creates a tab for the part, allowing for easy removal of the backing once the part is removed from the transparent liner and placed on a substrate.
The Difference Between Kiss Cutting and Die Cutting
In the converting industry, we often hear the term kiss cut used with die cut, but kiss cutting is a form of die cutting.
Die cutting is a process comprised of both through cuts (which pass fully through a material) and kiss cuts (which pass partially through a material), but both are necessary to construct adhesive parts.
For example, you might utilize a kiss cut to cut shallow sticker shapes on a sticker sheet for easier peeling, but to cut the sheet smaller, you’d use a through cut to cleave the whole paper in two.
The Advantages of Kiss Cutting
One of the most significant advantages of kiss cutting is its convenience. This method is excellent for arranging a high quantity of parts into individual groupings for commercially sold products.
HIGH-QUALITY PRODUCTION
Kiss cutting allows you to have firm control over the production process.
By making slight adjustments as the kiss cut pieces travel through the equipment, a converter can achieve tighter tolerances as they’re turned into roll form.
This process consolidates operations, allowing converters to manufacture more complex products in fewer steps. As a result, the machines don't continue running for as long, which saves time and money.
BETTER SHIPPING AND HANDLING
Kiss cut adhesives can be distributed to the customer in either roll form or sheet form, which results in more organized storage than loose parts.
Rolled products require less labor to transport and are significantly more cost-effective. Companies can also automate them for production straight off the shelf.
Rolled products experience minimal human contact from raw material to packaged product transformation, ideal in industries like medicine, where one might need to avoid cross-contamination.
EASIER USE
Another crucial point to consider is the actual application of the adhesive, which could be ideal for two reasons:
- Keeping the parts aligned in rows makes them easier to access quickly and transport on the job.
- Kiss cutting enables you to add features like the tab shown, which leads to better accessibility.
How Can Kiss Cutting Go Wrong?
When done incorrectly, kiss cut products will exhibit additional defects that hinder their use.
For one thing, the cut’s depth can make or break the product's functionality:
- A too-deep cut might cause the adhesive to seep into the kiss cut itself and "lock up" the delivery material or liner
- If the kiss cut is too shallow, the parts may appear fine to the naked eye, but when you remove them, they are nonfunctional as they are still stuck together
The tooling is very sensitive and requires close monitoring to ensure the exact cuts are made every time.
In addition, a defective kiss cut roll might be wound too tight or with inconsistent tension, triggering many potential issues, such as shifted parts or parts stuck to the backside of the delivery material, which could hinder automation.
What’s Next?
Kiss cutting is a valuable converting method that will enable other projects to run more smoothly as you get further down the road. But how will it function in your project?
Research is an excellent way to find the best production methods, but there’s nothing like having a replica of your design that you can test. If you’re hoping to try kiss cutting with one of your designs or materials, consider contacting a flexible material converter for a sample.
Otherwise, feel free to take a closer look at our Learning Center for more information on kiss and die cutting.
Originally published: July 12, 2022
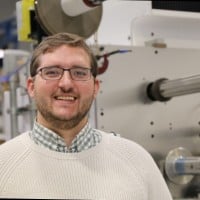