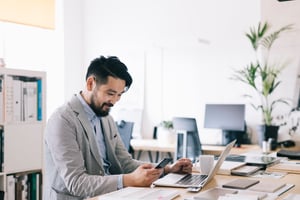
Optically Clear Adhesive
Crucial for Modern Electronics
Optically clear adhesive is used on display devices and touch panels to bind the plastic, cover lens, or other optic materials to the primary sensor unit to improve durability and optical characteristics.
Strouse die cuts optically clear adhesive to meet your custom format needs, including shapes and sizes.
HOW IT WORKS
Unlike other materials, optically clear adhesives are entirely transparent and uncolored and allow the entire surface area of a screen to bond to the device without any distortion to the graphics display.
The adhesive bonds to the touch panel and any productive cover to the touch screen. After the adhesive is applied to the electronic device, it’s cured using ultraviolet light, moisture, heat, or a combination of these methods.
Optical clarity is the most critical aspect of the adhesive. We all want displays that are transparent and easy to read, regardless of light conditions. As the use of optically clear adhesive expands to many applications (tablets, cell phones, touch screens, etc.), the demand for this valuable adhesive grows.
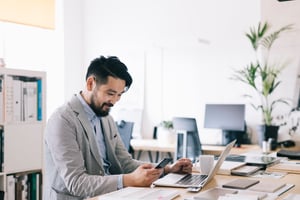
USES FOR OPTICALLY CLEAR ADHESIVE
Some specific uses of optically clear adhesive include:
• Bonding of flexible-to-rigid or flexible-to-flexible optical components for touch screens, flat-screen CRTs, and flat panel displays.
• Base film for optical components, as a screen surface protector, or as a sputter coating to resist harsh chemicals and scratches.
• Touch screens use the material to reduce flammability in medical, aerospace, and other similar industries.
• Bonding of backlight assemblies, A/R surface treatment films, holographic optical elements, diffusers, polarizers, and many other management films located in device displays.
For electronics screen bonding, it’s crucial to use tight tolerance die-cut parts. Otherwise, the application may have excess adhesive or contaminants around the device’s perimeter. The die-cut helps to create the most reliable bond while minimizing weight.
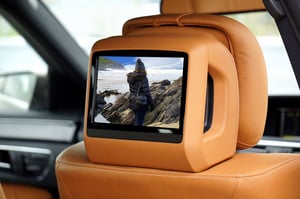
ADVANTAGES OF OPTICALLY CLEAR ADHESIVES
The use of optically clear adhesives helps improve device display performance. It effectively eliminates the gap between the LCD and cover glass, and it typically includes an anti-reflective coating, along with anti-glare and anti-smudge treatments for the cover glass.
Specific benefits of optically clear adhesive:
• Facilitates high light transmission
• High clarity
• Low haze
• Non-birefringent
• Virtually defect-free
• High adhesion
• UV protection
• Bare ITO compatible
• Whitening resistant
• Out-gassing resistant
• Temperature resistance
• Humidity resistance
• Excellent workability
• Manufactured in a cleanroom environment
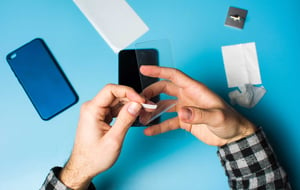
3M OPTICALLY CLEAR ADHESIVES
Strouse is experienced with all 3M optically clear adhesives, each designed to be used without any distortion of clarity and in applications where very high adhesion is critical.
Strouse converting includes slitting and die cutting (sheeted parts, parts on a roll). We also can add a tab to the part or extended liners, making it easy to remove the liner and place the adhesive.
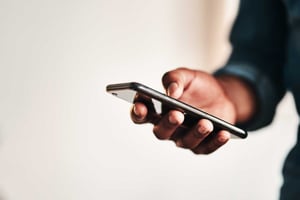
Whether you’re in the design stage or looking to spec in an optically clear adhesive part for your product, our engineering team can help.
