You’re on page 5 of 32 material selection pages… Getting sleepy yet? Rather than continue staring at nearly identical rolls of material, sit back and relax as we discuss whether silicone is the right choice for your application.
Silicone gaskets offer a wide range of heat-resistance and durability benefits, making them a popular choice for gasket manufacturing.
As a converter, Strouse regularly builds custom gaskets for our clients. We’re familiar with silicone’s material behavior compared to other gasketing materials, so today, we’ll explain its uses.
Read on to learn about the benefits and uses of silicone gaskets, plus what to consider when choosing a material for your gasket design.
What is a Silicone Gasket?
If you’re looking for multi-temperature range, high-performance mechanical seals with high resilience and durability, you should consider using silicone gaskets.
Silicone gaskets can withstand high and low temperatures, making them a highly versatile material. Use them when you need a material with high-temperature resistance, a low compression set, and good electrical insulation.
TYPES OF GASKETS
The type of material in your gasket depends on its intended use. For example, if you’re dealing with a rigid object, you need a gasket that fits the set shape. Doors and moving structures need something more flexible.
Before you design a gasket, consider your needs, including temperature, pressure, corrosion resistance, availability, and cost.
Gaskets must be solid so they don’t allow materials to pass through, and some need to handle energy discharge. You can have many different types of gaskets, including:
- Pipe gaskets
- Gasketing tape or adhesive
- Gasketing foam
And many different materials, including silicone, neoprene, EPDM, Teflon, Gore-Tex, and graphite gaskets.
What Are the Uses of Silicone Gaskets?
Because of their versatility, silicone gaskets are used in many different industries.
AEROSPACE
Silicone gaskets resist extreme temperatures, UV light, ozone, and chemicals. Because they can handle extreme weather and temperatures without wearing down, they’re often the right fit for airplanes, space shuttles, and similar vehicles.
TRANSPORTATION
Silicone gaskets are stable and durable, maintaining their resilience and strength even in extreme conditions. Because they can handle unnecessary stress without issues, they are great for personal, commercial, or industrial vehicles. In addition, they reduce vibrations, provide high-quality radiator seals, and are otherwise used for mass transit systems like buses and trains.
COMMERCIAL APPLICATIONS
In the construction industry, silicone gaskets seal HVAC systems and windows or doors. You can also use them in engine gaskets to vent ducts.
Other uses of silicone gaskets include sealing food processing machinery and industrial ovens in the food industry. The medical industry uses them for medical equipment like healthcare devices and pharmaceuticals.
What Are the Benefits of Silicone Gaskets?
Before we get into the different types of silicone gaskets, it’s worth considering the properties that differentiate them from other gasketing materials.
There are thousands of materials to make gaskets, but silicone stands out thanks to the benefits that allow it to be used in indoor and outdoor applications.
1. ABILITY TO WITHSTAND HIGH AND LOW TEMPERATURES
Silicone gaskets can withstand temperatures up to 392 degrees Fahrenheit continuously, which makes them great for many industrial applications. It can be exposed to high heat levels without degrading or wearing out.
Silicone seals can also withstand heat up to 428 degrees Fahrenheit intermittently and withstand extremely cold temperatures, remaining flexible at as low as -94 degrees Fahrenheit.
2. EXCELLENT INSULATION
Silicone gaskets have conductive capabilities that make them excellent insulators of electricity. Blending silicone with nickel-graphite or silver-plated aluminum particles can shield electromagnetic interference (EMI).
Silicones are found in most high-voltage insulators and other electrical components. Different chemical reactions can cross-link them, making them non-reactive at high temperatures. The electrical industry relies on these non-reactive materials. Silicone can also be blended with semi-conductive carbon to prevent electromagnetic discharge.
3. HIGHLY DURABLE
Silicone gaskets are highly durable and resistant to UV light, ozone, and extreme weather conditions, making them ideal for outdoor gasketing.
Plus, silicone's tensile strength and durability make the gaskets highly economical, as it is a reliable and stable material. You can use these gaskets for a long time without them showing wear, and once installed, they don’t require much maintenance.
4. FDA APPROVED
Because silicone gaskets are FDA-approved, they can be used in medical equipment, health care instruments, and food processing plants. They can also be mixed with other FDA-approved materials for high tear strength.
Unlike asbestos gaskets, silicone gaskets are also physiologically inert (not toxic or harmful to people). Their high tear strength and inertness make silicone gaskets useful for healthcare, food processing, medical diagnostic equipment, and pharmaceuticals.
5. COMPRESSION SET RELIANCE
Compression set reliance means that silicone gaskets function well under pressure by returning to their original thickness even after being compressed for long periods.
Silicone gaskets are a smart choice for a lower compression set. A compression of 100% means the material will never return to its original thickness. Lower compression set reliance materials ensure the material doesn’t get deformed in certain temperatures.
Matching the compression set reliance of your material to your intended use is essential. If the gasket material deforms, the seal will fail, leading to leaks and contaminations.
6. FLAME RETARDANT
Silicone gaskets have low flammability levels, making them ideal for industries that generate excessive heat. They can also be used in telecommunications equipment and mass transit systems.
Silicone gaskets meet Underwriters Laboratories (UL) testing requirements for fire safety and flame resistance, meaning they can achieve UL94V0, UL94V1, and UL94HF1 flammability standards.
7. WATER-REPELLING MATERIAL
Silicone gasket material is water-repelling, repelling liquids, resisting moisture, and maintaining a watertight seal. This sealing ability is essential for industries dealing with moisture or water and is great for outdoor use in wet weather conditions.
What Are the Types of Silicone Gaskets?
Silicone gaskets can come in sheets or rolls of different thicknesses. Depending on your needs, you can also use solid, sponge, or foam silicones.
TYPE #1: SOLID SILICONE GASKETS
Solid silicone gaskets are not always soft but rather tightly packed and more rigid than sponge silicone. If you need a seal rating of IP67 or higher, you’ll want to choose solid silicones.
Solid silicones can offer exceptional sealing capabilities, but remember that they’re challenging to compress because of their hardness and require 15 to 20% compression.
TYPE #2: SPONGE SILICONE GASKETS
Sponge silicone gaskets offer more cushioning and padding. They can be open-cell or closed-cell. Open-cell silicones contain pockets that allow water, air, and chemicals to pass unless the gasket is compressed.
Closed-cell silicones have pockets filled with nitrogen to prevent water, air, or other chemicals from passing through, even at low compression. They will need at least 50% compression. Sponge silicone gaskets have a higher temperature threshold of 500 degrees Fahrenheit.
TYPE #3: FOAM SILICONE GASKETS
Foam silicone gaskets can be soft, medium, firm, or extra-firm and offer different compression levels. Like sponge silicone gaskets, foam silicone gaskets need at least 50% compression. They can be open-cell, closed-cell, or a mixture of both, and their temperature threshold is 400 degrees Fahrenheit.
TYPE #4: DIE CUT SILICONE GASKETS
Die cut silicone gaskets are a common type of gasket, built using custom machine tools to create unique parts.
If you’re using your design with custom sizes and thicknesses, die cut silicone gaskets could be a good option. They’re often a more economical option for large volumes, because thousands of die cut gaskets can be produced per hour.
TYPE #5: MOLDED SILICONE GASKETS
Molded silicone gaskets provide a higher-performance seal than die-cut silicone gaskets. However, this might come at a higher upfront cost, even though both are good for high-volume production.
TYPE #6: CONDUCTIVE SILICONE GASKETS
Conductive silicone gaskets are made up of a mix of high-quality silicone and conductive particles. They are filled with conductive materials like nickel, carbon, and silver-plated nickel and are used for electronic equipment.
TYPE #7: FDA (FOOD GRADE) SILICONE GASKETS
FDA-approved silicone gaskets are generally used in the food processing industry. They are odorless, tasteless, and fungus-resistant. They also can handle extreme cold and heat, making them ideal for places with food around, like dough or cake mixers.
TYPE #8: FLUOROSILICONE GASKETS
Unfortunately, silicone isn’t ideal for oil or petroleum-based chemicals. Fluorosilicone, or fluorinated silicone rubber, is similar to silicone, except it can withstand extreme temperatures and resist fuels, oils, and other petroleum-based chemicals.
Silicone Gaskets vs Rubber Gaskets
Choosing between a silicone and a rubber gasket will depend on your goals. Silicone gaskets can be more efficient and perform better than rubber gaskets, especially in extremely high temperatures.
Natural rubber can work well in temperatures from -58 degrees to 176 degrees Fahrenheit intermittently, whereas silicone can handle more extreme temperatures, from -94 degrees to 426 degrees intermittently. Natural rubber starts to wear down at 176 degrees and melts by 248 degrees.
The cost of rubber materials like SBR can make them more appealing than silicone in pricing. However, rubber is not used with ozone, strong acids, fats, oils, and grease. Silicone, on the other hand, can be used with these materials. You can use silicone gaskets in UV and extreme weather conditions for outdoor applications.
Ultimately, you’ll want to consider your design and application before finalizing your product material, which leads us to…
Choosing the Right Gasket Material For Your Solution
Now that you know more about silicone gaskets, you’re ready to pick out a gasket adhesive that suits your needs. Moreover, given the complexity of material behavior, you’ll want more to go off of than simply matching the numbers on a data sheet.
Before you finalize your design, you might want to test the material within your application. Requesting a design sample will allow you to see if silicone really is the best choice for your gasket design.
It’s one thing to build the perfect gasket once, but how can you consistently manufacture your part to reduce the chances of product failure?
We’re here to help you through your product development process. Reach out to ask questions or request a sample. Lastly, please visit our Learning Center for additional resources.
Originally published: February 24, 2022
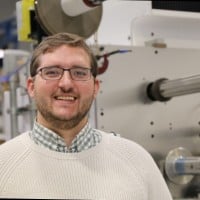