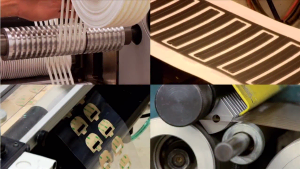
JOINING, MOUNTING, AND BONDING ADHESIVE SOLUTIONS
Bond Similar and Dissimilar Substrates
A variety of materials — adhesive film, adhesive tape, glue, epoxy — can be used to join together two or more surfaces. We’ll help you select the right ones for your project, then use our industry-leading capabilities to deliver the finished products you need.
Our solutions are also designed to streamline the assembly of custom products. The right bonding tape (3M VHB and acrylic foam tapes) can even replace rivets, welding, and fasteners, evenly distributing the pressure throughout the area of the tape as opposed to small points along the substrate.
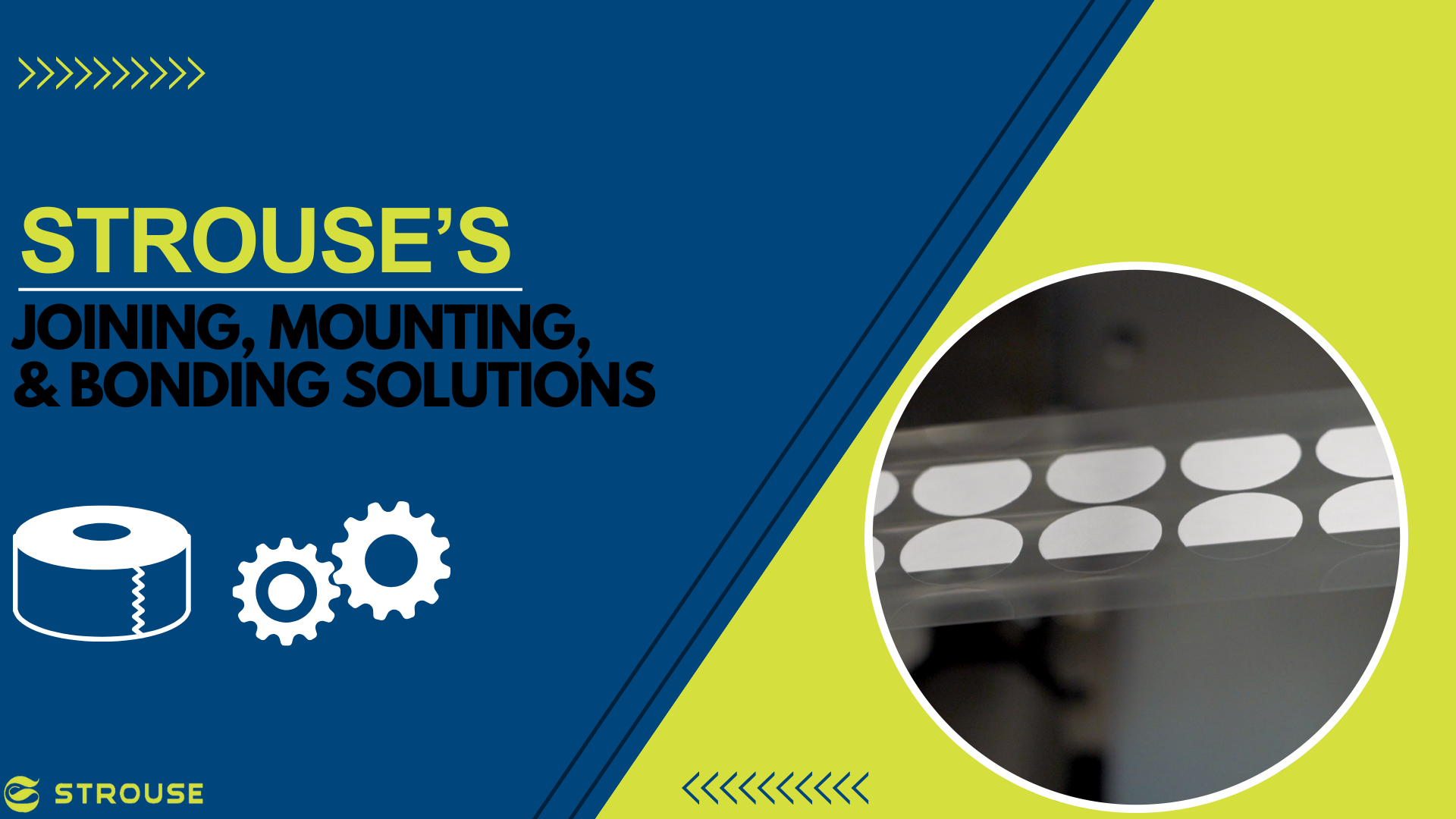
Adhesive bonding uses a viscous substance to combine two or more surfaces. This process joins the surfaces together temporarily or permanently through the creation of a smooth bond.
The different materials manufacturers use:
• Adhesive film
• Adhesive tape
• Glue
• Epoxy
Temporary bonding tape, also called “removable tape” or “repositionable tape,” has strong holding properties but can easily be removed or repositioned. Use this tape on reclosable packaging, removable or changeable gaskets, and other products that require temporary holding.
If you have a unique requirement that’s not yet available, Strouse can build it. For instance, if you need permanent adhesive on one side and removable on the other, ask Strouse.
- Better Stress Distribution — When a single strip of adhesive film connects two substrates along the entire bond line, the force becomes more evenly distributed and shear strength improves.
- Stronger Protective Seal — A mechanical fastener is no longer needed to create a physical seal between components; adhesives create a secure coverage that works like a seal.
- Expanded Surface Area — When manufacturers use adhesive bonding to fill or pot a space, they create a more secure and structurally sound connection.
- Improved Appearance — Binding tape creates a tight connection without adding unsightly bulk to the components.
- Power To Join Different Materials — Because of its versatility, adhesive bonding creates a secure bond between surfaces that aren't the exact same.
- An Innovative Future — Robotic systems apply adhesives using automatic adhesive dispensing to make the entire assembly line more efficient, accurate, and consistent.
In years past, traditional films tended to be weaker than other binding materials. Thanks to bonding innovations, they're now some of the most durable materials on the planet. In fact, most modern films now use self-curing adhesives to create bonds that are nearly as strong as the components themselves.
It’s now possible to combine even the toughest materials together. If you've ever wondered how to bond metal to metal without welding, this approach offers one solution.