/Delta%20ModTech%20Edge%203.jpg?width=300&name=Delta%20ModTech%20Edge%203.jpg)
Industries
Put Our Experience To Work For You
You are the expert in your industry, yet we likely can contribute something you haven’t yet considered. For instance, we've used insights from the electronics industry to create an innovative medical solution. That’s the advantage of partnering with Strouse.
Review our list of the primary industries to which we contribute. When you have the experience and diverse manufacturing capabilities that we do, it’s natural that we’ve delivered adhesive solutions across various markets.
Aerospace
Quieter. Lighter. Damage-resistant. Equipment in the world of aerospace engineering has constant demands to meet.From die cut adhesive solutions to pressure sensitive tapes to durable film materials, our solutions are counted on to serve critical functions, prolong longevity, and enhance the quality of these materials. Partner with Strouse on all project types, from untested concepts and short runs to full-on manufacturing of proven solutions.
- Top manufacturers — NASA, Boeing, Northrop Grumman, Lockheed Martin — all rely on Strouse for various aerospace adhesives:
- Chemical Stripping Protection
- Noise, Vibration, and Harshness
- Moisture Barrier
- Heat Shield
- Surface Protection During Refurbishing
- Fire Retardant Sealant
- Kick Plate Panel Securement
- Extreme Surface Protection from Rocks and Debris; Belly Tape
- Carpet Installation Tape
- Seat Cushion Attachment
- Vehicle Masking
- Masking Kits
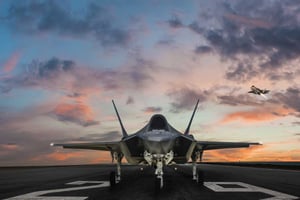
Appliance
Appliance industry professionals need adhesive products that solve two main challenges. The first is to create an aesthetically pleasing look, with little to no damage done to the product’s surface. An attractive, polished finish is vital.
The second, of course, is to adhere to substrates as needed. Depending on the appliance, additional functions could include providing noise reduction and/or thermal insulation, protecting components from moisture, and preventing damage to a surface during production or transportation.
Your source for appliance adhesive tape solutions is Strouse. We design tapes that meet your functionality needs: component marking, surface protection, mounting, injection, transport, and more. Our adhesive tape solutions enhance whatever appliance being produced:
- Refrigerator
- Freezer
- Oven
- Dishwasher
- Washing machine
- Dryer
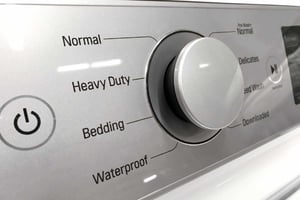
Automotive
Saving time and money on the assembly line is a huge advantage. Strouse’s diverse manufacturing capability allows us to slit automotive adhesive to the sizes you need, cut them to shape, create a tab, or extend the liner for easy hand assembly.
Being a 3M Preferred Converter makes 3M automotive adhesives easily accessible. Plus, Strouse has a quality management system registered to ISO 9001:2008 standards to ensure that each project is held to the highest quality standards.
Top manufacturers — Ford, Tesla, Chrysler, Honda — all rely on Strouse for various automotive adhesives:
- Gaskets and Sealing
- EV Solutions
- Paint Masking
- Bonding Solutions
- Part Mounting
- Buzz, Squeak, and Rattle Protection
- Mutilation Protection
- Transit Protection
- Surface Protection
- Hole Covers
- Security Labeling
- Vibration and Sound Deadening
- Masking Kits
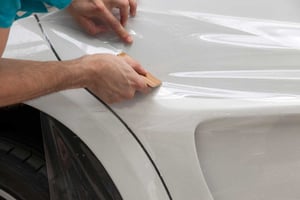
Consumer Goods
Manufacturers in the consumer goods industry are experiencing more complex and varied demands every day. Strouse’s high-end adhesive tapes enable the production of a variety of consumer-focused products: keypads, beauty care products, fashion products, furniture, sport and leisure equipment, and many more.An extensive and comprehensive list of adhesives covers many applications for consumer goods. The need drives the solution: instant adhesives, large surface area bonding, anaerobic adhesives, flexible adhesives, and tapes with high adhesion capabilities.
Want to improve an existing product?
Want to develop a new product?
Our experience creating custom adhesive solutions can help. We’ve developed solutions that meet the needs of nearly every combination of material and in almost every application area.
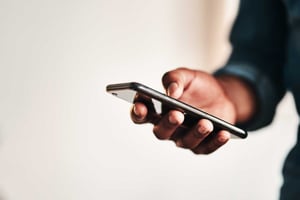
Design & Construction
Performing under demanding environments and tough conditions is the main benefit of an adhesive solution for the design and construction industry. Not only do they need to have superior adhesion strength, but they also must help improve productivity, reliability, safety, and be convenient to use. Strength is important, yet working when they’re cold or on wet surfaces cannot be overstated.
From new construction to renovations, Strouse can help at any stage of your project. Our innovative and rugged products are used for a variety of applications.
Various tapes and adhesives:
- Vinyl Electrical Tape
- All-weather, Corrosion Protection Tape
- Rubber Splicing Tape
- Self-fusing Silicone Rubber Tape
- Rubber Mastic Tape
- High-temperature Masking Tape
- Fire Barrier Tuck-in Wrap Strips
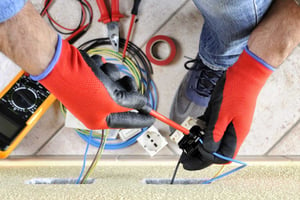
Electronics
As electronic devices continue to decrease in size, the need for smaller, more efficient components with multiple functions becomes critical. Strouse is a 3M Preferred Converter, with access to 3M electronics materials, including:
- Optically clear adhesives that allow you to bond touch screens without the use of hardware, reducing weight and stress
- Thin thermal bonding solutions to dissipate heat while securing a heat sink to circuity
- EMI shielding and RF absorbing products
Our electronic adhesive solutions include:
- Thermal Management
- Bonding Solutions Including using Repositionable Adhesive that can Eliminate Waste
- EMI Shielding
- Conductive Adhesive
- Screen Protection
- Flat Screen and LCD Screen Bonding using Optically Clear Adhesive
- Heat Sink Attachment
- Insulation
- Gaskets
- High-Temperature Labels
- High-Temperature Insulation
- Solder Masking

Industrial
With a wide range of applications, industrials often require adhesive products in customized sizes to fit specific pieces of equipment or even new products.
Strouse has access to the most advanced industrial tape and adhesives on the market: bonding tapes, grip materials, hook and loop attachments, and many more. We convert flexible materials to custom sizes and shapes, providing unique features for each application. If solutions are needed for hand assembly, we manufacture a product with a tab or extended liner, making it much easier to apply.
Top manufacturers — 3M, GE, Procter & Gamble — all rely on Strouse to die cut industrial tapes and adhesives:
- Permanent Bonding
- Temporary Bonding
- Fasteners
- Surface Protection
- Paint Masking Solutions
- Gasketing
- Gripping
- Sealing
- Packaging Solutions
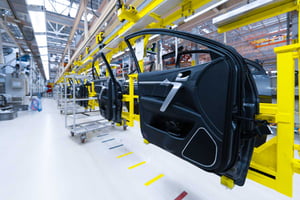
Medical
A medical device normally has multiple goals: performance, compliance, cost, and timelines. All are important, and all are dependent on the adhesive you use. Strouse adhesive engineers treat each medical device as its own unique product, creating converting solutions with a focus on how that device will perform in the long-term.
Choosing an adhesive for a medical application usually is determined by its use. What needs to be done?
- Hold device components together
- Cover a device
- Move fluid
- Stick a device to skin
- Deliver an active ingredient through skin
Unlike every other industry we serve, being a 3M Preferred Converter isn’t quite enough. Strouse is also a 3M Preferred Converter of 3M Medical Materials and Technologies, a rarity among the thousands of U.S. converters.
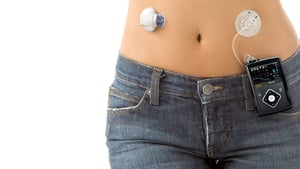
Military
Whether it’s refurbishing used equipment, building new machinery, or tracking weapons and vehicles, adhesives serve as a critical component to ensure successful military operations.
Our position as a 3M Preferred Converter of pressure sensitive adhesive and flexible materials gives Strouse access to the most advanced materials on the market: acrylic foam tapes, flame retardant materials, hook and loop attachments, masking tapes, reflective material, and many more.
Top organizations — the Army and Marines, SAIC, Honeywell, Northrop Grumman, Lockheed Martin, Defense Logistics Agency — all rely on Strouse for die cut adhesive applications:
- Paint Masking Kits for Refurbishing Humvees
- Equipment Attachment
- RFID Tag Attachment
- Thermal Management Components
- EMI and RFI Shielding
- Heat Sink Bonding
- Conductive Adhesive Components
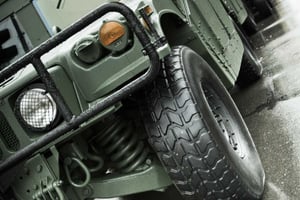
Renewable Energy
Renewable energy systems — solar, wind, geothermal, nuclear, batteries — all use adhesive tape products in their manufacture and/or installation. Our engineering, R&D, and sales pros have experience providing applicable solutions to the renewable energy industry’s unique challenges.
Strouse is directly connected to the world’s leading suppliers of advanced films, tapes, and adhesives, with the ability to supply products around the world. We’re proud to help our environment by offering products that enhance sustainable solutions.
Strouse’s renewable energy tape applications:
- Conductive Foil Tapes
- Dielectric Insulating Tapes
- Epoxy Adhesives
- Foam Mounting Tapes
- Installation Tapes
- Labels
- Laminating Adhesives
- Liquid Adhesives
- Mirror Film
- Optically Clear Adhesives
- Polyester and Protective Films
- Reclosable Fasteners
- Structural Adhesives and Sealants
- Thermal Interface Materials
- VHB (Very High Bonding) Tapes
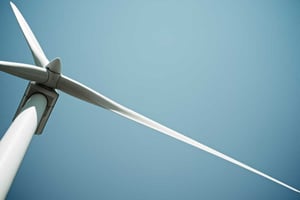
Safety
From personal protective equipment (PPE) to occupational health and safety posters, signage, placards, and labels, Strouse’s diverse manufacturing capabilities and pressure sensitive adhesive solutions are used to help promote and ensure safety.
Strouse proclaims that we’re “More Than Tape,” so we’re producing face shields to meet recent demands for reliable PPE. We didn't just design a face mask with a soft foam headband and anti-fog PET. We designed a fully automated process on our presses to speed up the production, which allows us to produce more of them faster as demands dictate.
Strouse believes in, and lives, workplace safety, even achieving 1,000 consecutive days (3 years) with no lost time accidents in our own facility.
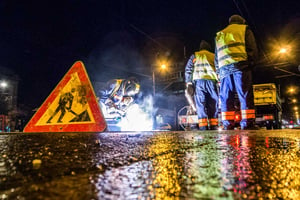
REQUEST A QUOTE

Provide us details in the form and we can get you a quote for your product.
- What Product Are You Looking For?
- What Size/Dimensions?
- Quantity You Will Order
- Information on How the Material Will Be Used
- Problems You May Have Encountered When Using this Material