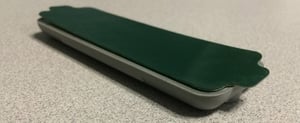
Acrylic Foam Tape
About Acrylic Foam Tape
Acrylic foam tape is used in applications that require high-performance attachment including automotive bonding, medical device component attachment, gasketing, and much more. This adhesive foam tape can create bonds strong enough to replace screws, rivets, welding, and other permanent bonding solutions.
Acrylic foam tapes are high strength, flexible, and resilient foam adhesive that enables engineers and manufacturers to solve functional needs like permanent bonding while also improving the performance of their product or simplifying assembly. These added values provide real ROI for your adhesive components and increase your margins.
Converting Foam Tapes
Strouse converts acrylic foam tapes and other pressure sensitive adhesives to custom sizes, shapes, and formats. We provide rolls of tape slit to custom widths or foam tape components cut to custom shapes and dimensions. These components can be provided in multiple formats including wound on a roll, on singular sheets of liner, or as individual pieces with a liner to protect the adhesive. These fomats are designed to simplify your assembly process, so whether you apply foam tape components by hand or machine automation, Strouse can design a solution that is customized to fit in with your existing processes.
MANY CAPABILITIES. ONE CONVERTER
IMPOSSIBLE
130% PRODUCTION IMPROVEMENT
Applications & Use Cases
Acrylic Foam tapes are used in almost every industry. Medical manufacturers use foams to bond medical device components together or to secure dressings directly to skin while providing cushioning. The automotive industry is using foam tape for sidewall panel attachment on commercial vehicles, truck bodies, and public service vehicles. Thin foam tape is used in the electronics industry to bond assemblies and attach LCD and touchscreens.
Strouse die cuts and converts foam tape and flexible materials to solve many different adhesive applications. Our diverse manufacturing capability allows us to provide you the material you need in the exact size, shape, and format required for your design.
Popular Acrylic Foam Adhesive Tapes
Strouse sources acrylic foam tapes from leading suppliers including 3M, Avery Dennison, AFTC, and many others. We have over 75,000 rolls of material and more than 2,000 individual materials in stock at any given time. If you're looking for a specific material, just ask, but here are some of the most popular:
- 3M™ Acrylic Foam Tape 4220
- Avery Dennison AFB 61 Series Tape
- Avery Dennison AFB 62 Series Tape
- Avery Dennison AFB 64 Series Tape
- Gaska V1520 Series (Medium Density)
- and More!
Strouse die cuts and converts foam tape and flexible materials to solve many different adhesive applications. Our diverse manufacturing capability allows us to provide you the material you need in the exact size, shape, and format required for your design.