Despite the furious whirring of my laptop whenever I boot up a videogame with too-high FPS, it hasn’t burst into flames yet; which is, in part, thanks to its thermal conductive pad.
As you already know, certain pieces of technology become extremely hot when running, so devices such as laptops require a system to drain the heat. Components like thermal conductive pads are essential facets of heat management systems that prevent device failure.
Strouse has spent over three decades building thermal conductive pads alongside other critical components for electronics. If you’re looking into finding them for your product, you’ll want to ensure you get thermal conductive pads with suitable materials, specifications, and more.
To help you be more successful with thermal conductive pads, we’re going to dive into the details, from giving a broad thermal pad definition to how you’ll find the right manufacturer for a custom job.
What are Thermal Conductive Pads?
Thermal conductive pads, commonly found in electronic devices, are used to bring heat away from the primary source and spread it across more areas of a device. The thermal pad’s conduction aids other components, such as heat sinks, and provides a cooling effect to reduce the chances of system overload.
How Do Conductive Pads Work?
The thermal pad material conducts and distributes heat across another surface, such as the underside of a heat sink, to prevent the temperature from overloading the system and causing a failure. Soft conductive pads will also conform to uneven surfaces and fill spaces to improve thermal performance.
Thermal conductive pads function within integrated chip (IC) packaging, chip on film (COF) dissipation, technological gap filling, and facilitate heat transfers from printed circuit boards (PCBs). Manufacturers also use adhesive pads in electric vehicle (EV) batteries, LED displays, sensors, wireless charging devices, and many other applications.
Thermal Conductive Pad Materials
Just as with any other part component, a thermal conductive pad’s material composition is heavily influenced by its intended purpose, design, and part application.
Due to a wide range of adhesive options, it’d be challenging to select a material without knowing what substrates the conductive pad is bonding to.
For instance, all of these materials could be used in different thermal conductive pads:
- Thermal tape
- Silicone foam
- Graphite sheets
- Ceramic fillers
It’s crucial to understand that thermal conductive pad materials tend to fall on the more expensive side of flexible materials due to their specialization.
In addition to the base price, these materials often come in smaller rolls, which affects how an operator sets up a machine press and how often they need to perform roll changes. This means you’ll end up paying more for the process steps as well as the material.
Small rolls of expensive materials often result in adhesive converters using setup materials to calibrate a die cut press. The minimum setup material length might be around 30 feet, whereas more complex designs (those involving more materials, different cuts, and more laminations) could require the purchase of additional setup material to get the press properly attuned before running smaller, more expensive material rolls.
Smaller rolls also mean that the operator will spend more time changing out the material than they would if the material consisted of longer rolls.
Manufacturing Factors to Consider in Thermal Conductive Pad Design
Whether or not your design is complex, multiple factors might affect the price and timeline of your thermal pads if not accounted for properly.
#1. MATERIAL SELECTION
What if I asked you to write me a letter, then handed you a brick to write on?
Using the correct materials is an essential distinction between conductive pads that thrive and ones that don’t. Besides functionality, material selection also makes a massive difference in the ease of production.
There are two things to consider for manufacturability:
- Whether the material comes on a roll
- Whether it has a supportive backing
Materials that come on a roll will be easier to run on die cut press, while materials that come in sheets are often thicker and may contain netting or other alternative layers.
Similarly, supportive backings or liners contribute to manufacturability. Soft or gooey materials will be more challenging to cut, which may result in higher manufacturing costs. However, adding a structural backing can mitigate some of these struggles.
#2. THICKNESS
The thickness of a thermal pad will vary wildly depending on your intended purpose and design. For instance, smaller devices might require thinner, more lightweight thermal conductive pads, while larger applications might need thicker, space-filling material. Either way, just know that an extremely thick material, especially one that’s multi-layered, could reduce the ease of production.
#3. QUANTITY
Thermal conductive pads are often produced for very specific purposes, so quantities tend to be lower than other part components (often somewhere in the hundreds). This is also mainly due to the high cost of material, which could be thousands of dollars per a few hundred feet depending on the material complexity.
#4. PAD APPLICATION
In terms of design, a one-layer part in a square shape will often be easier to manufacture and apply because they’re simpler. These thermal conductive pads tend to be applied to the PCB, and if they have adhesive on them already, a manufacturer can just stick them on.
Some heat sink pads might need to be added using heat activated adhesives, solder, or some type of additive. In certain cases, you might also consider additional die cut features such as tabs or split liners to improve the ease of application.
Conductive Pad Alternatives
There are multiple alternatives to conductive pads, including thermal paste and glue. These conductive adhesives work in applications where you need to eliminate all microscopic air gaps, which won’t be possible in the case of thermal pads. Depending on the chosen material, they also might suffer less natural degradation than a thermal pad over time.
However, in instances where the heat sink needs to be held together by the interface material, a bonding material like a thermal pad will likely both function better and can be pre-cut to size for a less messy, more standardized application.
Finding Thermal Conductive Pads
As you’ve probably noticed, finding a thermal conductive pad depends on the type you’re searching for.
If you’re looking for a simple design using a common material, it’s far more likely that you might be able to source them online— especially if you’re searching for a very small number of parts. However, if that isn’t the case, it might be time to consider a flexible material converter.
For more customized designs, specialized materials, or larger part quantities, you’ll want to consider contacting an adhesive converter.
An adhesive converter will help you adjust your design to be more manufacturable, source materials, and create prototypes to test your thermal conductive pads.
Feel free to reach out for a project consultation if you’re interested in pursuing a project, or you can read more about thermal interface materials in our Learning Center.
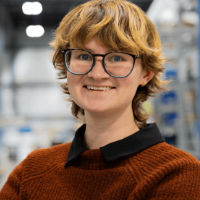