You might ask yourself, “How can I improve my adhesive strength?”
However, there’s more to establishing a successful adhesive bond than upping the strength of your tape.
Strouse has been helping bring adhesive components from the design stage to production for over three decades now, and we’ve been approached by countless companies encountering product development issues.
Suppose your adhesive is failing, or you’re hoping to prevent adhesive failure. The following tips will inform you of the potential pitfalls to help you successfully choose an adhesive and lower the chance of adhesive failure.
What Causes Adhesive Failure?
There are many different reasons why an adhesive might fail.
The reason your adhesive fails could be entirely separate from the reason another part does. However, for clarity’s sake, we will place adhesive failure under two primary considerations: bonding ability and application.
BONDING ABILITY
The actual adhesive strength of your material depends on the compatibility of its adhesive bond. Above all else, you’ll want to check and ensure that your substrates (or surfaces you’re attaching) are compatible with your adhesive.
If a single tape worked on every surface, we’d use it for everything. As it stands, you must choose an adhesive that matches your substrates.
Another reason bonding ability might fail is due to the object’s weight or surface texture and curvature.
Attaching tape to a flat, horizontal surface is far easier than attaching it to a spherical surface. Similarly, textures make it easier for the adhesive to seep into the surface and create a stronger bond, whereas smoother surfaces have lower surface energies.
Certain surfaces, like those covered in powder-coated paint, have extremely low surface energies. Low surface energies make it challenging to bond adhesives and may require specialized adhesives or corona surface treatment.
APPLICATION
Although a component has a strong adhesive bonding ability, it won’t necessarily withstand additional factors adding stress to the bond.
For example, underwater submersion, heavy dust or dirt, or movement could cause the adhesive to detach.
Another question is how long you intend your application to last. High bondage materials like 3M VHB tape can endure years of outdoor weathering, but other adhesives might not.
You can help prevent adhesive failure by ensuring those involved in the material selection process know how, where, and for how long someone is applying an adhesive. Although the adhesive choice is critical, the part size and the stresses involved upon application will significantly affect its performance.
Why is MY Adhesive Failing?
As previously mentioned, there are multiple reasons why your adhesive might fail. Yet, looking at it from a business and production standpoint, there are three primary factors to consider.
#1: USING THE WRONG ADHESIVE
Bond failure often indicates an adhesive choice that doesn’t suit the substrates or application.
The fact is that every adhesive can be used for a specific purpose. If the tape fails, then it’s not the best material choice, length, et cetera for your project, and it becomes a matter of finding one that is.
Without the right adhesive, your part is bound to fail. But how do you find the right one?
You might have it all planned perfectly on paper, but it might not work as expected once you finally use the material within your part.
There are tens of thousands of rubber and acrylic adhesive variations, all with slightly different chemistries from one another. Theoretically, you could break down the science to a molecular level to find the perfect adhesive for your part, but then you’d be left struggling to produce the formula on a large scale. Instead, it’s more common to:
- Find the basic requirements of what you need
- Look for products with those characteristics
- Test the adhesive within your design.
STROUSE TIP: If the issues occur before or during assembly, consider switching to a high or low tack liner. Adhesive liners come in different strengths, and if the assembly is your issue, you might be using a suitable adhesive with the wrong liner.
#2: INSUFFICIENT TESTING
Companies run tests using materials and samples. However, there are still times when testing falls short.
Suppose you wanted to attach a large metal clock to a wooden board: you would no doubt choose a double sided tape with the ability to stick to metal and wood.
When it came down to testing, would you use wood you had on hand to prove your adhesive or take the time to find a wide piece that could adequately mimic the stress of the actual thing?
Depending on the sample, even the product batch size could change how your adhesive functions. Converters strive to get sample parts as close to actual production as possible, but there is always a risk of variation.
It's challenging to determine whether it'll work in context without trying the component how it’s supposed to be used. Replicating the surface areas, the type of stress your tape will endure, and accurate samples are essential during adhesive testing.
#3: LACK OF CONTEXT
“Why did our product fall apart?” asks the customer.
“We didn’t know you intended to drop it off a three-story building.” the converter responds.
Choosing an adhesive that will realistically function requires a lot of context.
If you’re building a part for production, your flexible material converter will help you choose an adhesive based on price and requirements. Highly durable materials cost more, and if your part must endure high temperatures or other extreme forces, you’ll want to warn your converter so they can help locate a suitable adhesive.
How Do I Prevent Adhesive Failure?
You can help prevent adhesive failure by planning your product process, conducting sufficient tests, and providing context.
First, consider the adhesive's primary purpose and how it’s failing that objective. Is it meant to stick permanently or semi-permanently?
Are there any adverse conditions to account for (UV light, rain, fire, high or low temperatures, wind, chemicals, types of sterilization, things brushing up against it, etc.)?
Think about the application. Does the tape mount an object on the wall, or is it withstanding a different type of adhesive force (sheer, peel, cleavage, etc.)?
Second, you’ll look at your adhesive options to find one that suits your product. This is a great time to loop in a converter or manufacturer to bring them up to speed on your product design for material recommendations or sampling.
At last, you’ll want to test your design with accurate samples alongside the other product components.
Are you hoping to prevent adhesive failure in your project? Maybe you’ve even encountered issues and are now stuck in testing limbo. Consider reaching out for samples or a design evaluation today:
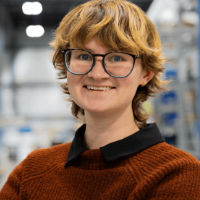